Das 0,6m Newton Projekt.
Nun, es ist mal wieder soweit! Ich habe beschlossen, der Sternwarte ein Teleskop mit mehr Öffnung zu gönnen. Warum auch nicht, immerhin passt da noch was Größeres unter die Kuppel und im März 2014 hatte ich das Glück einen sehr preiswerten komplett unbearbeiteten 600mm Suprax Spiegelrohling erwerben zu können.
Bis zum fertigen Teleskop mit Gabelmontierung ist es natürlich noch ein weiter Weg, doch ein Anfang ist gemacht und auf dieser Seite werde ich meine Bemühungen dokumentieren.
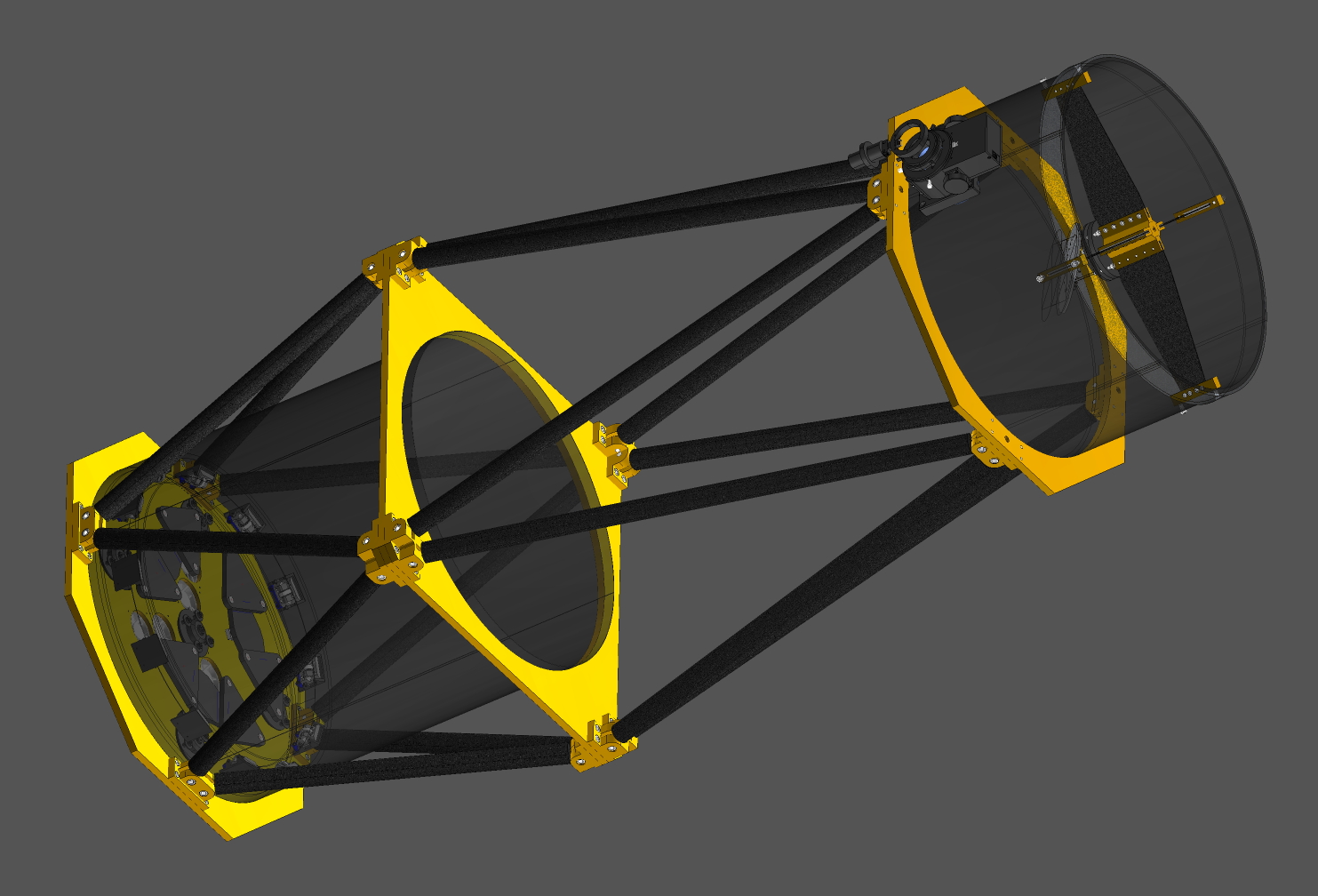
Seit einiger Zeit habe ich an einem Modell des neuen Teleskops gearbeitet. Nach dem mehrere Ansätze der Delete-Taste zum Opfer fielen, bin ich bei V8.21 angekommen und sehen nun nach reichlich Überlegung keinen Optimierungsbedarf mehr. So wird's gebaut!
Die Fangspiegeleinheit
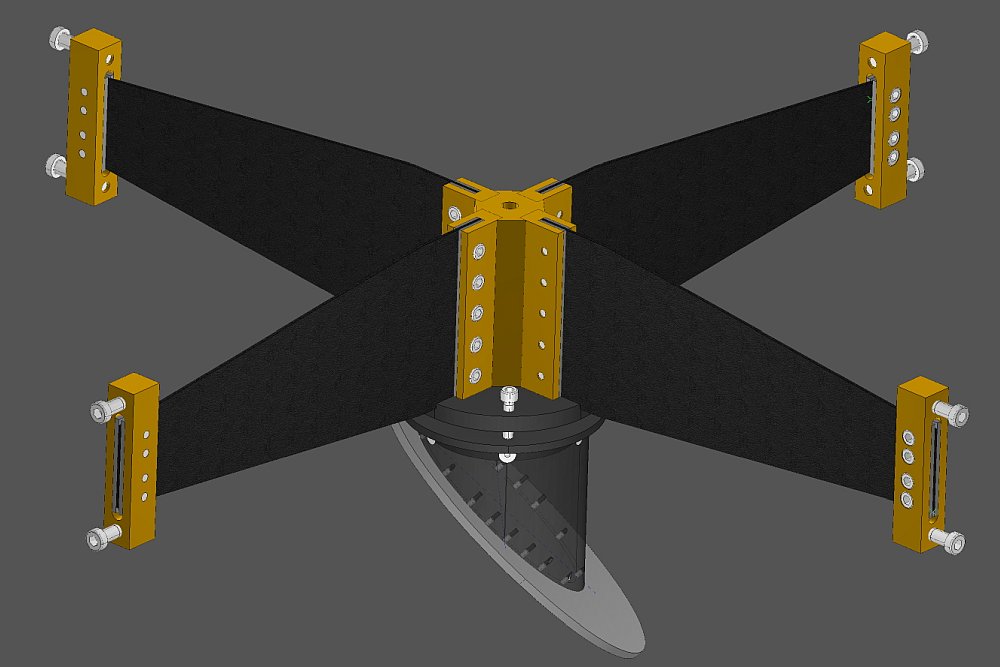
Der Sekundärspiegel wiegt 1,4kg und darf sich im tube nicht von der einjustierten Stelle bewegen. Die Fangspiegeleinheit sollte also sehr stabil aber auch fein justierbar sein.
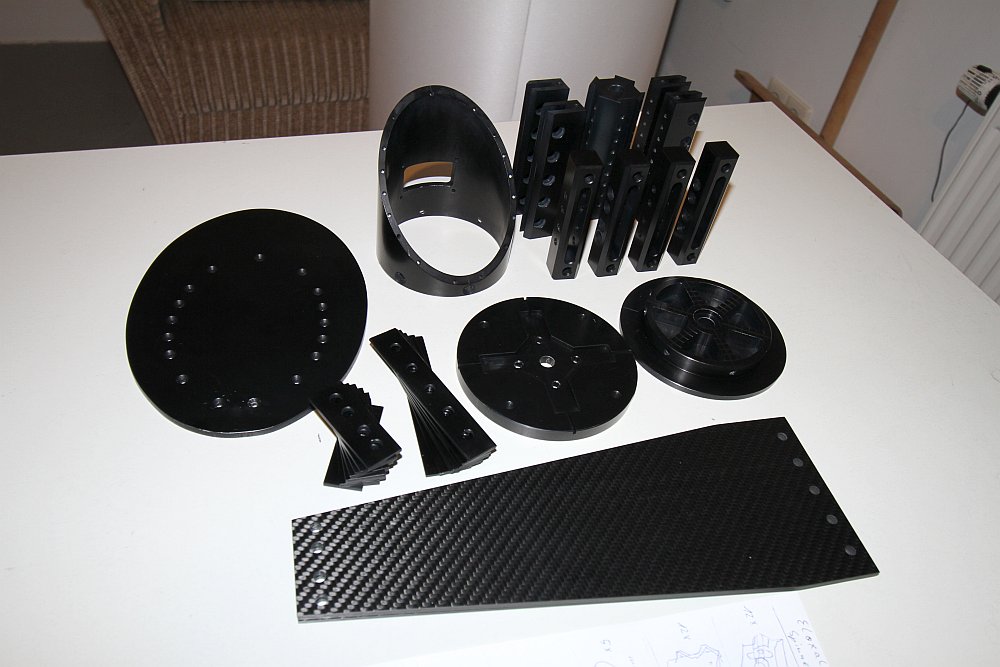
Die Teile fertig gefräst und eloxiert - habe mich doch im letzten Moment für die Farbe Scharz statt Gold entschieden. Die Fächer der Spinne bestehen aus 2mm CFK.
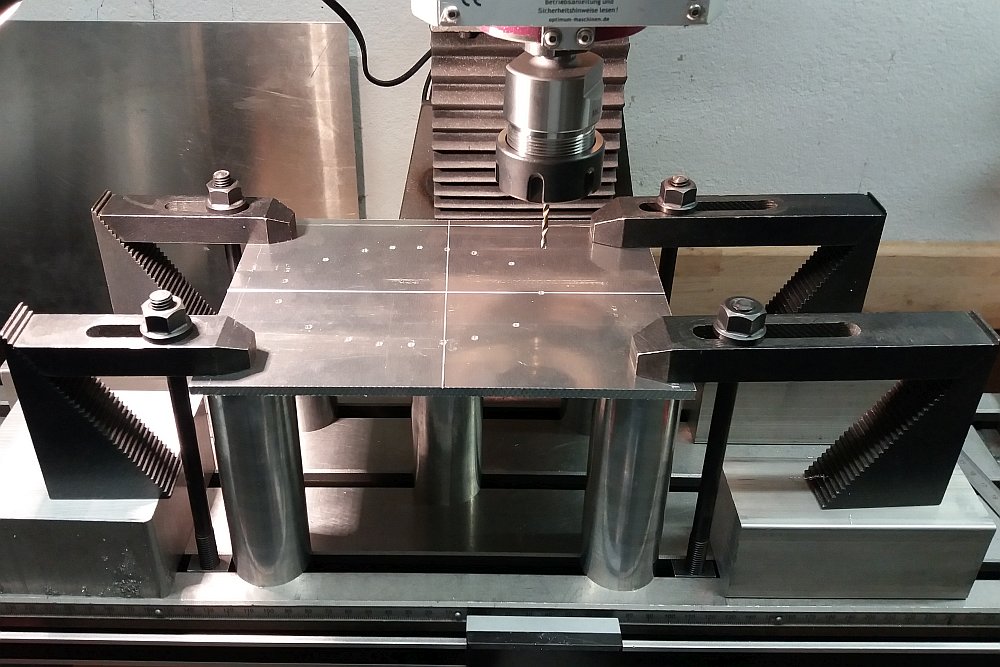
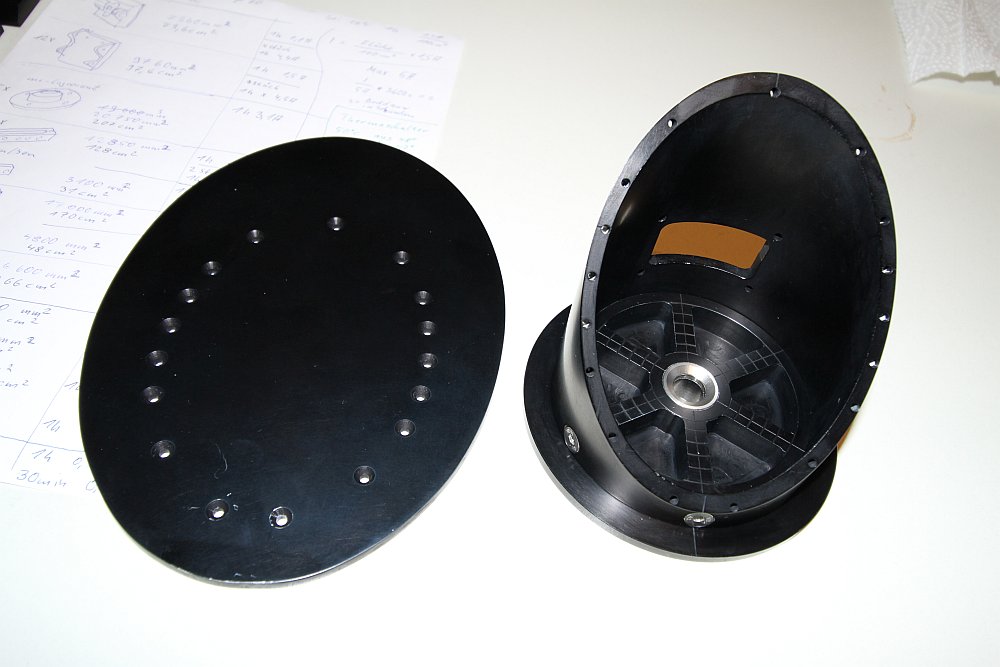
Fertig eloxiert.
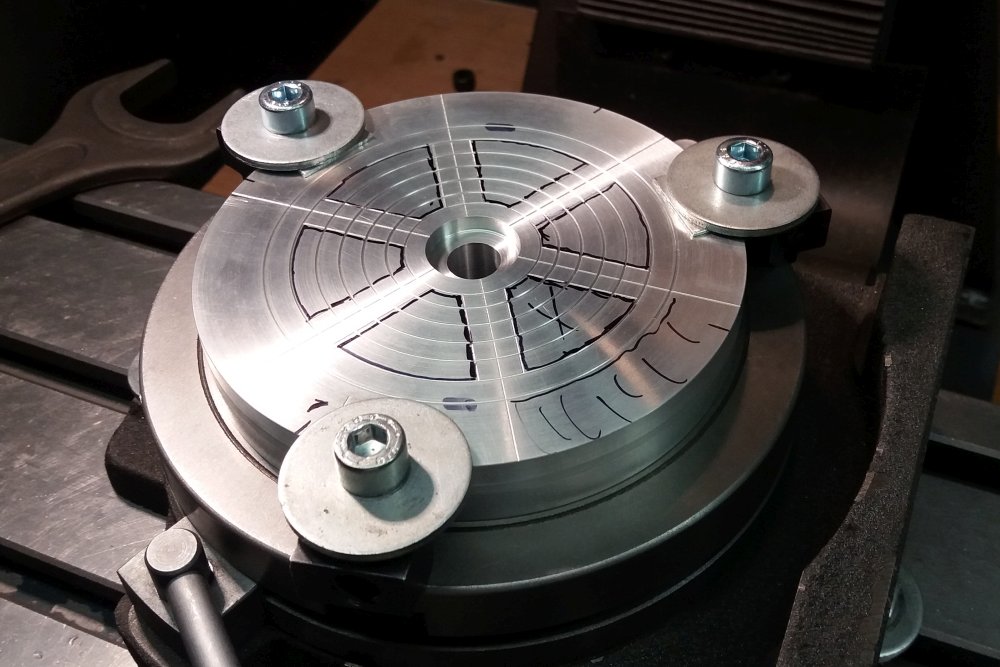
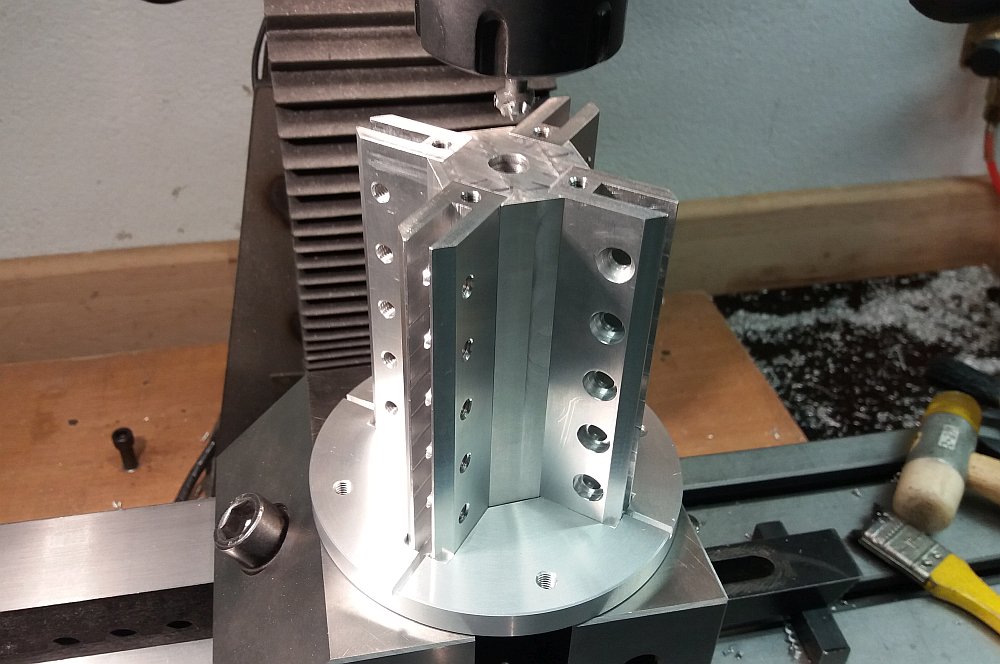
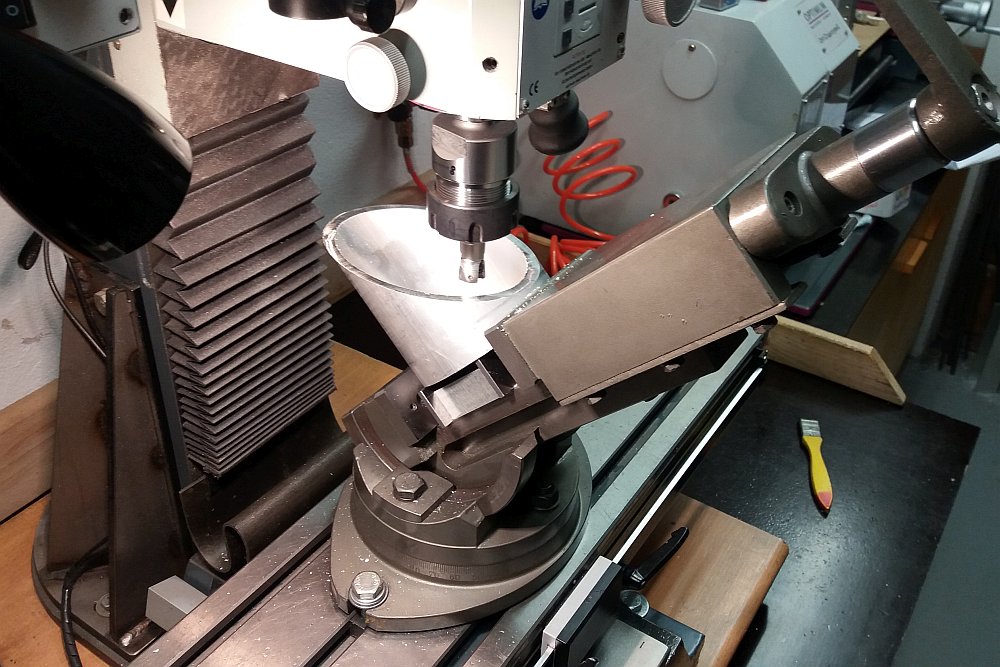
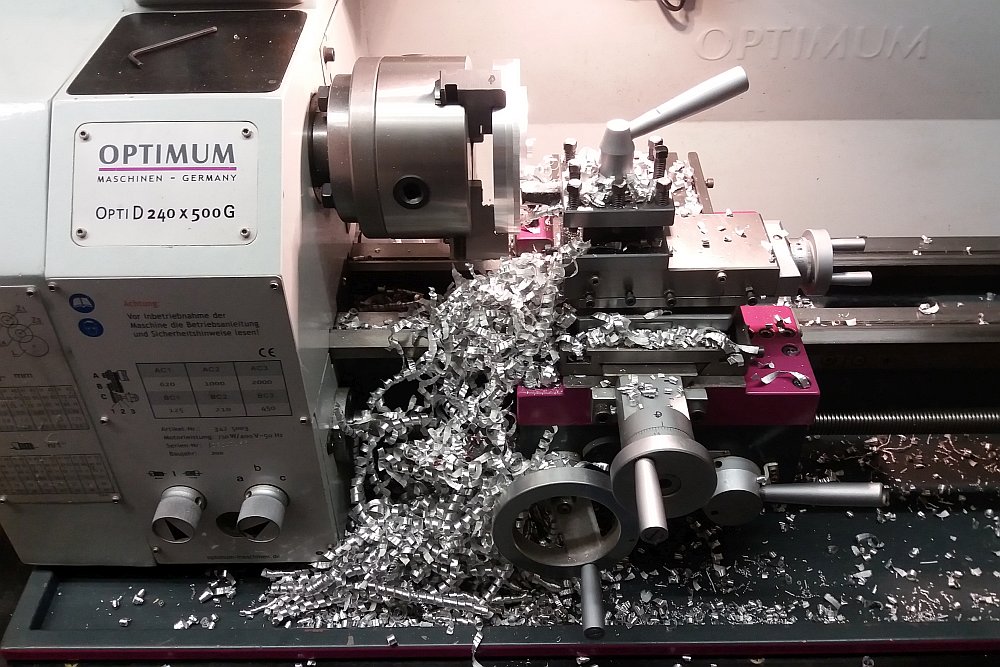
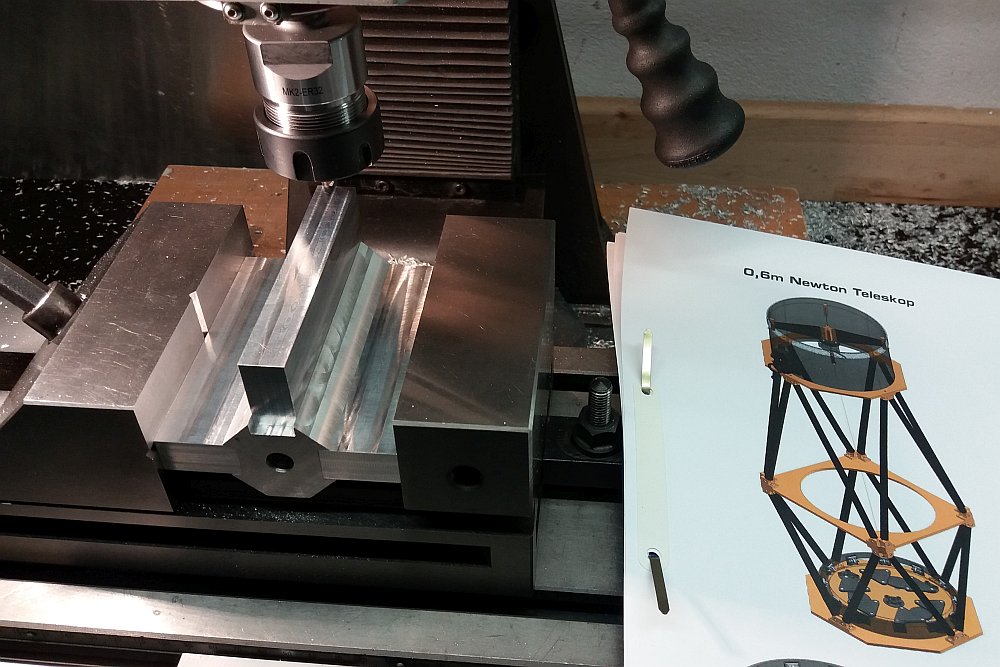
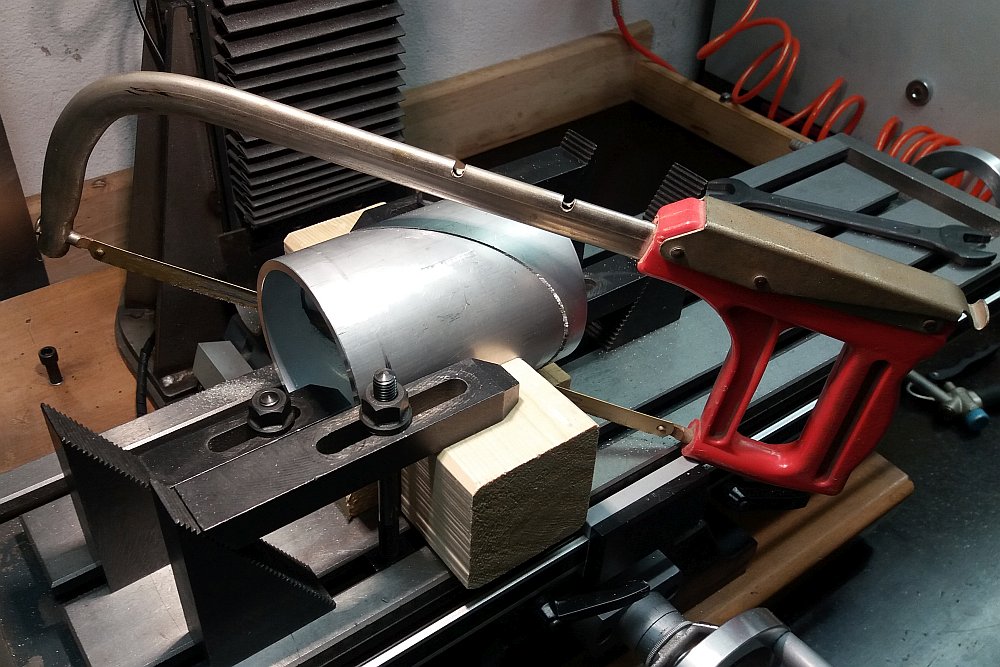
Der Gitterrohr Tubus
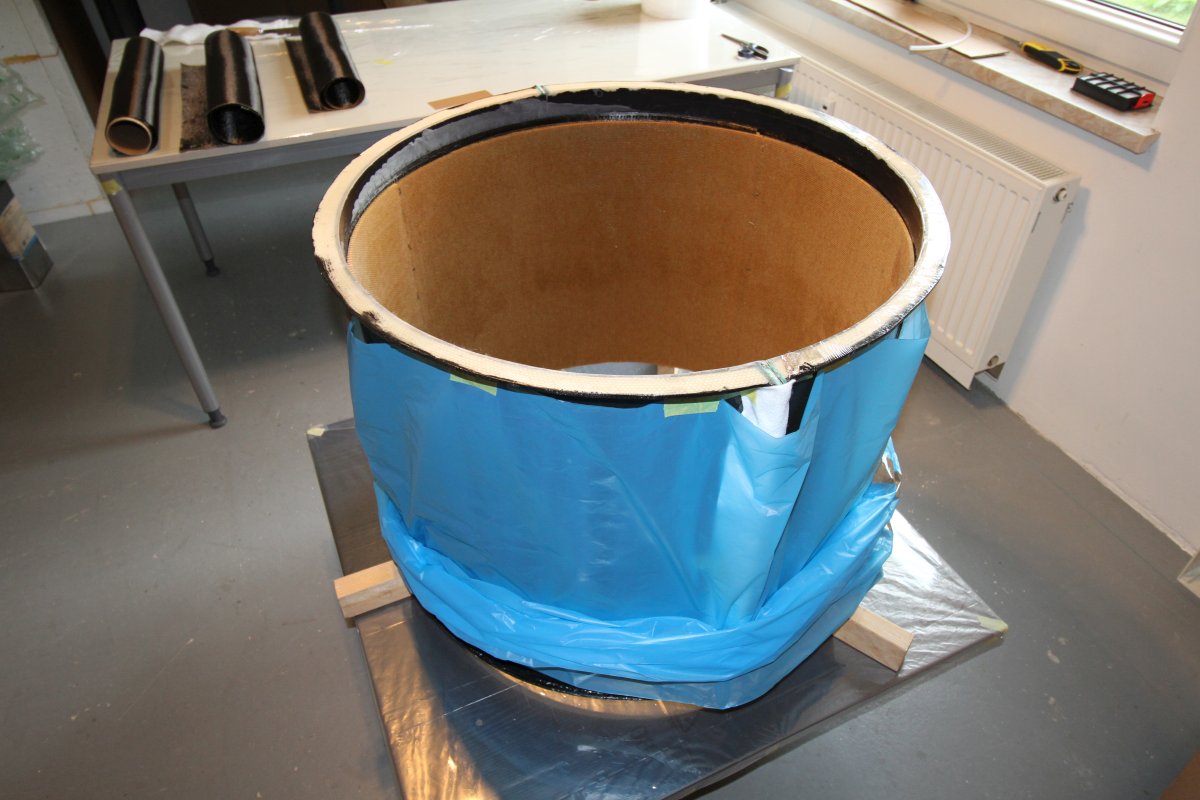
Nun habe ich mir mehr Mühe mit der Vakuum-Folie gegeben, alle Schnittstellen doppelt verklebt. Jetzt kommen noch mal die gleichen Schichten Kohle über die Waben und ein Abreißgewebe. Dann noch das ganze Vakuumgedöns.
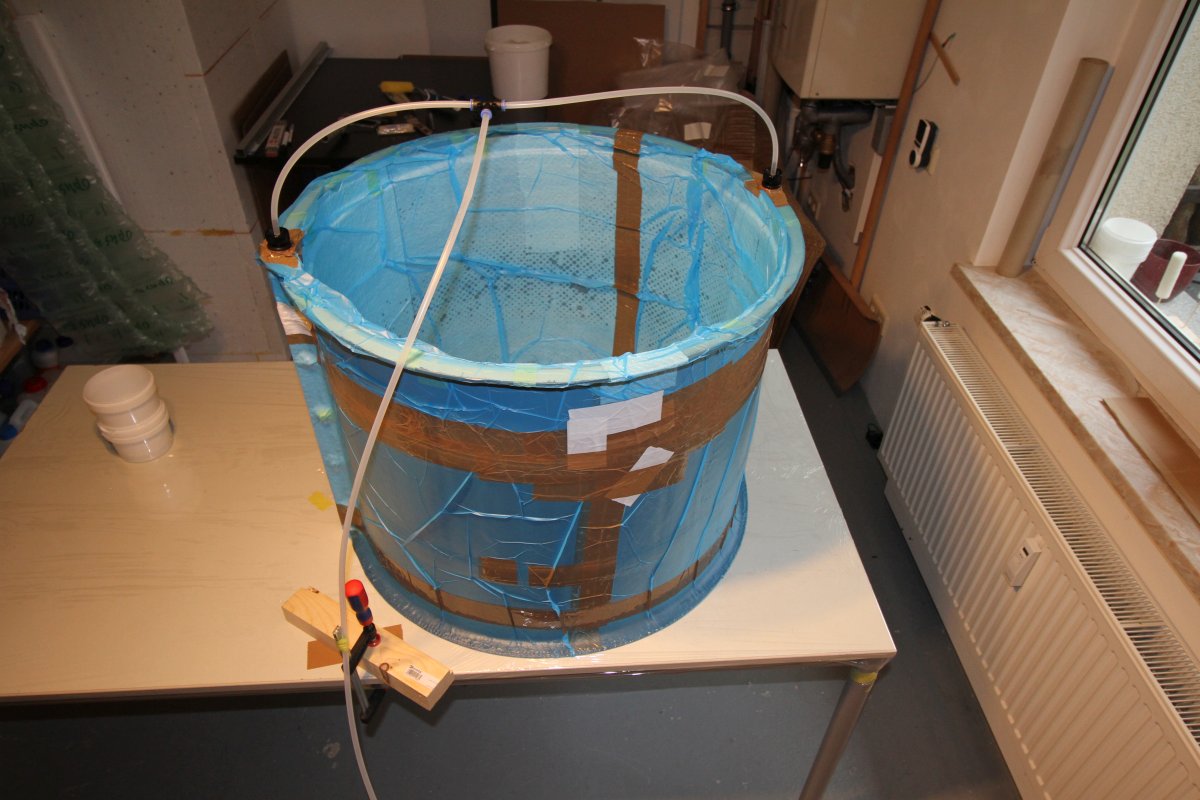
Nach 5 hektischen Stunden ist alles an seinem Platz und der Vakuumsack ist dicht. Nun kann die Membran Vakuumpumpe noch gemütlich 20 Stunden Luft ziehen. Das Mano zeigt stabil -300mBar - ist OK für mich.
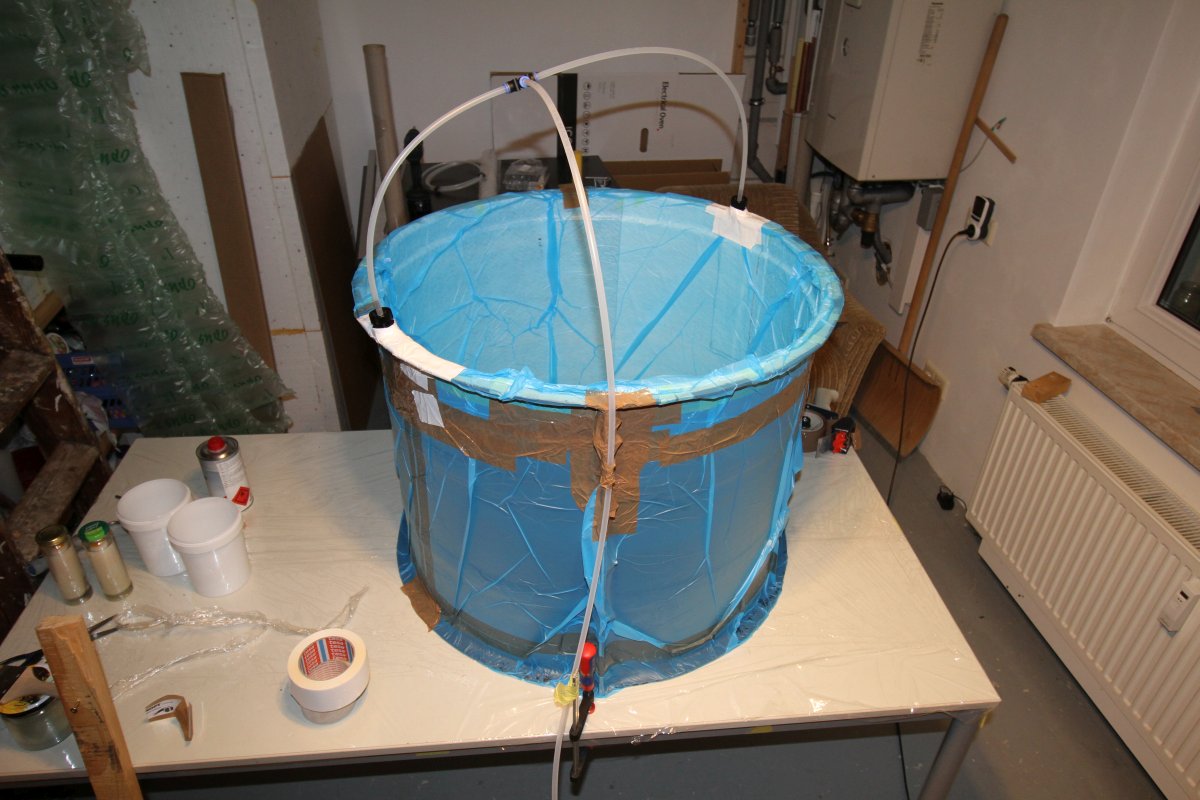
Das CFK muss beim aushärten gut durch Unterdruck gepresst werden. Leider habe ich die Folie hier nicht 100%ig dicht bekommen, so dass die Membran-Vakuumpumpe einfach nicht hinterher kam. Also musste mein Staubsaur den Part der Vakuum Pumpe übernehmen! Das Ergebniss war erstaunlich gut, aber der Staubsauger ist in den 20 Stunden Dauerlauf sicher zeitraffergealtert!
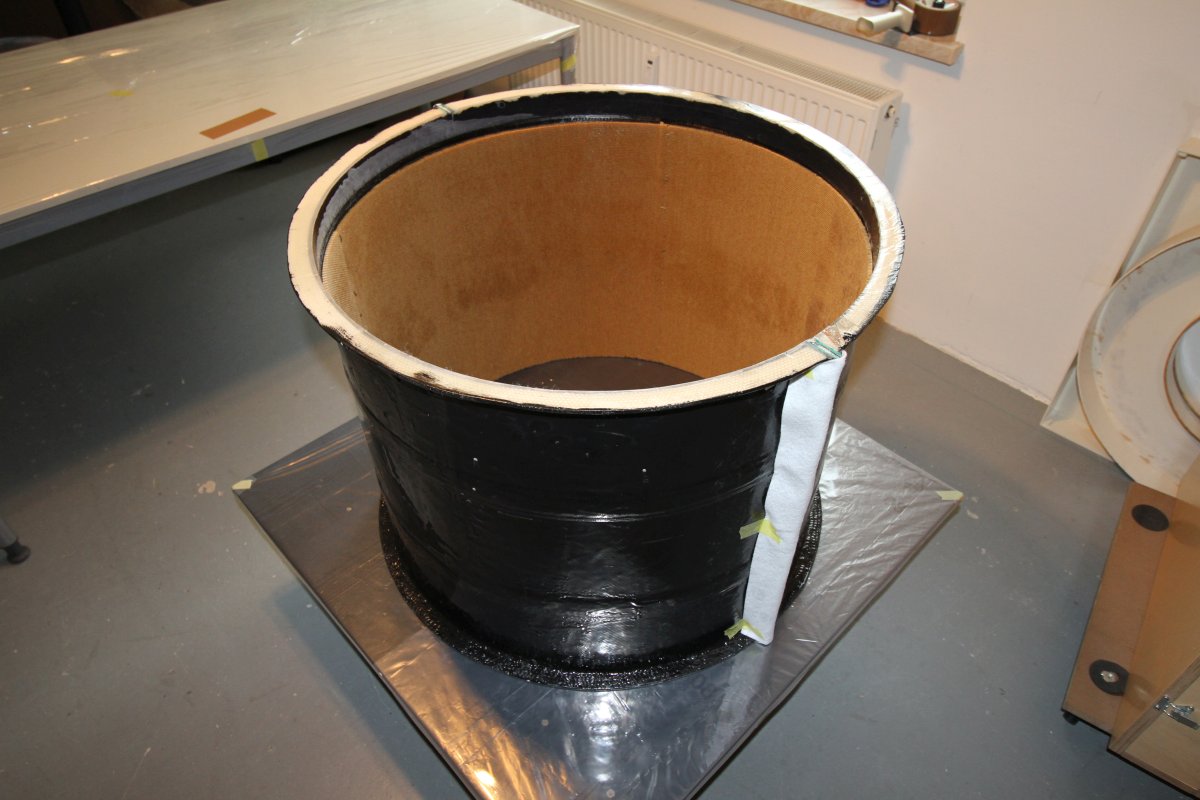
Schon in der Form:
1 Schicht Kohle Leinen 160g/m²
2 Schichten UD 400g/m²
1 Schicht Kohle Leinen 160g/m²
5mm Aramid Wabenkern
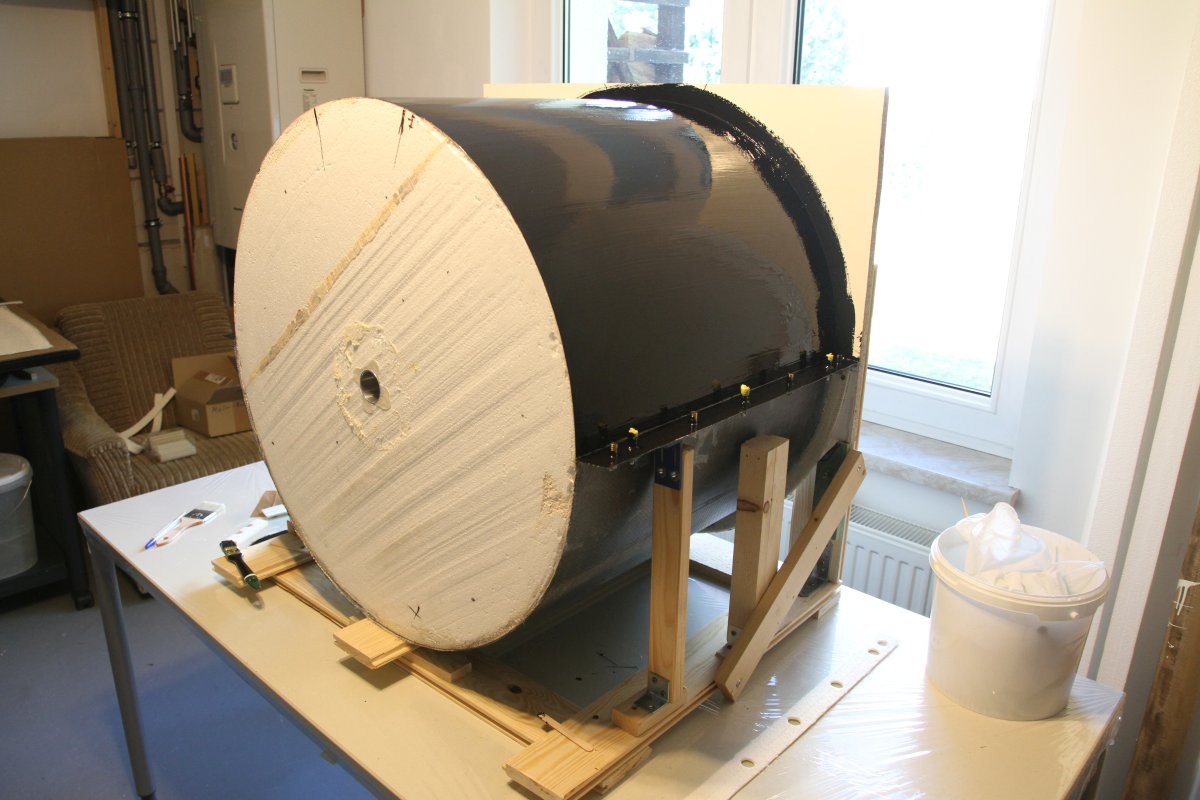
Die zweiteilige Form ist fertig.
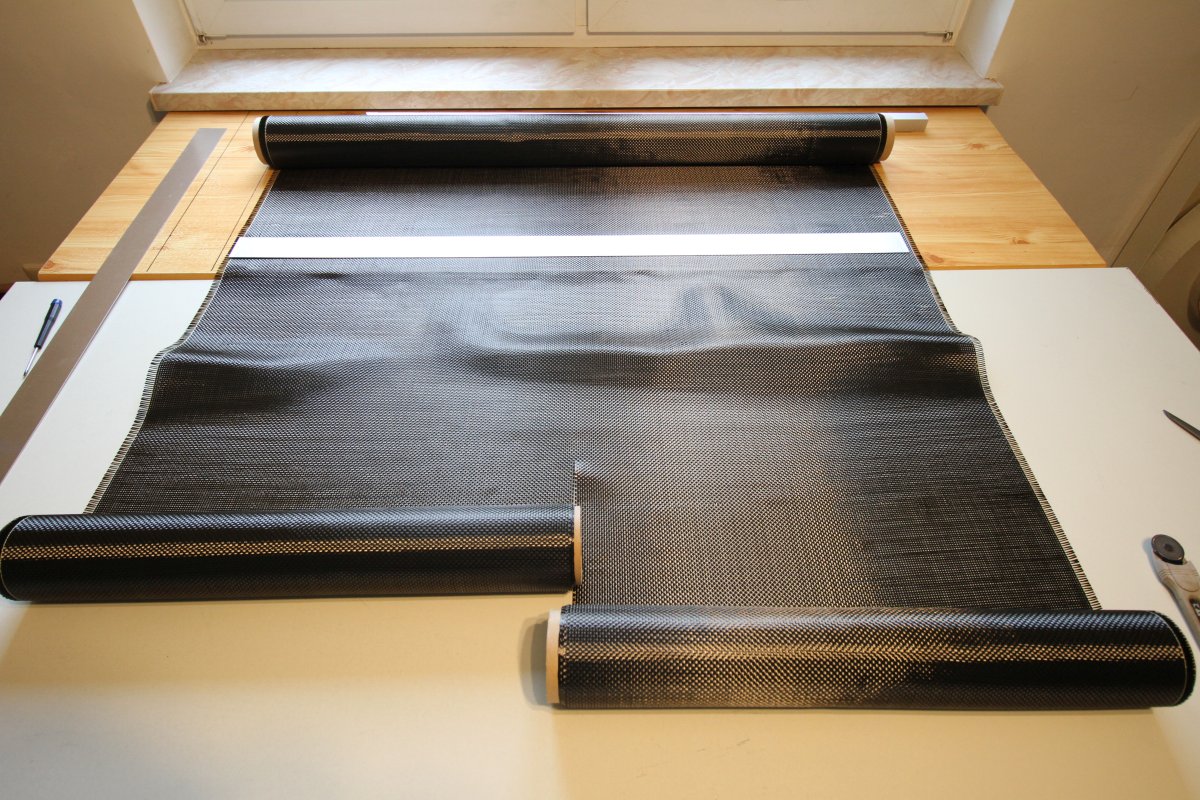
Das Zuschneiden und Aufrollen der verschiedenen Kohlefaserlagen ist immer etwas frickelig...
Die Fasern des Gewebes fallen fast von selbst auseinander.
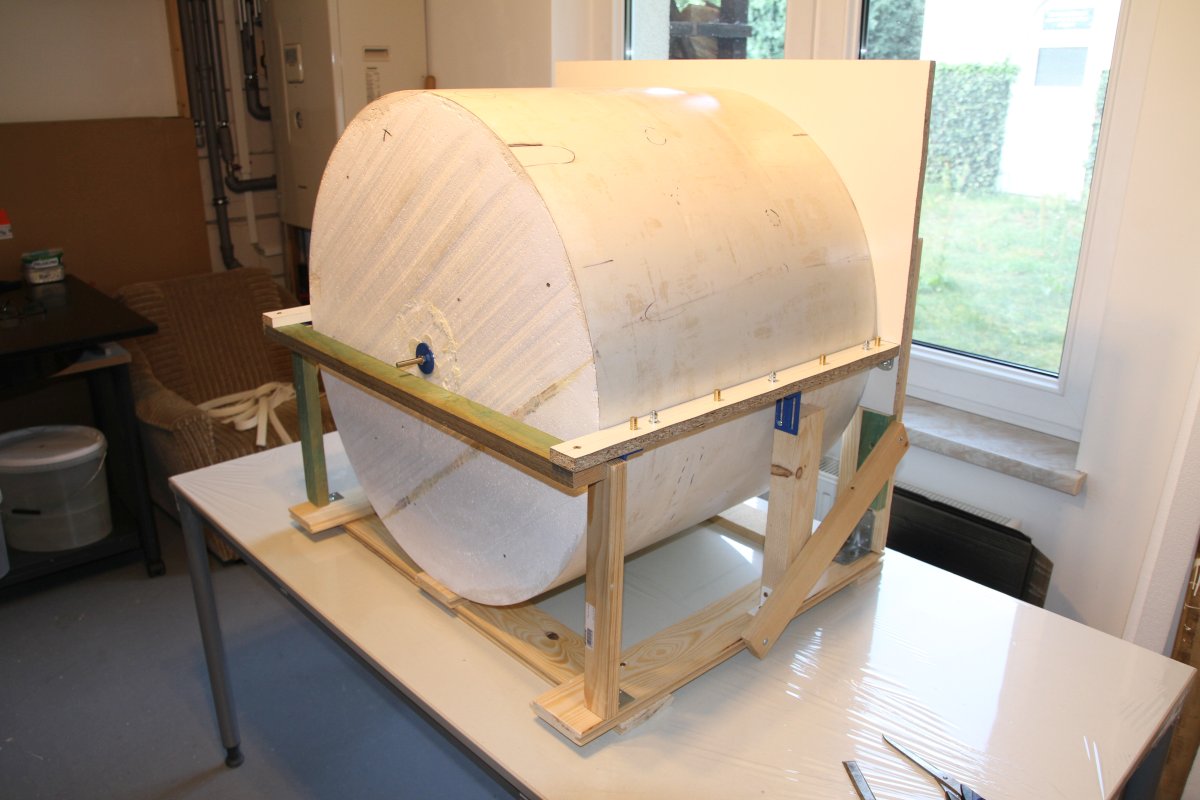
Um etwas Stabilität der Oberfläche zu erzeugen, wurden noch ein paar Schichten GFK aufgezogen und mit Spachtelmasse und Schleifpapier bis k240 geglättet.
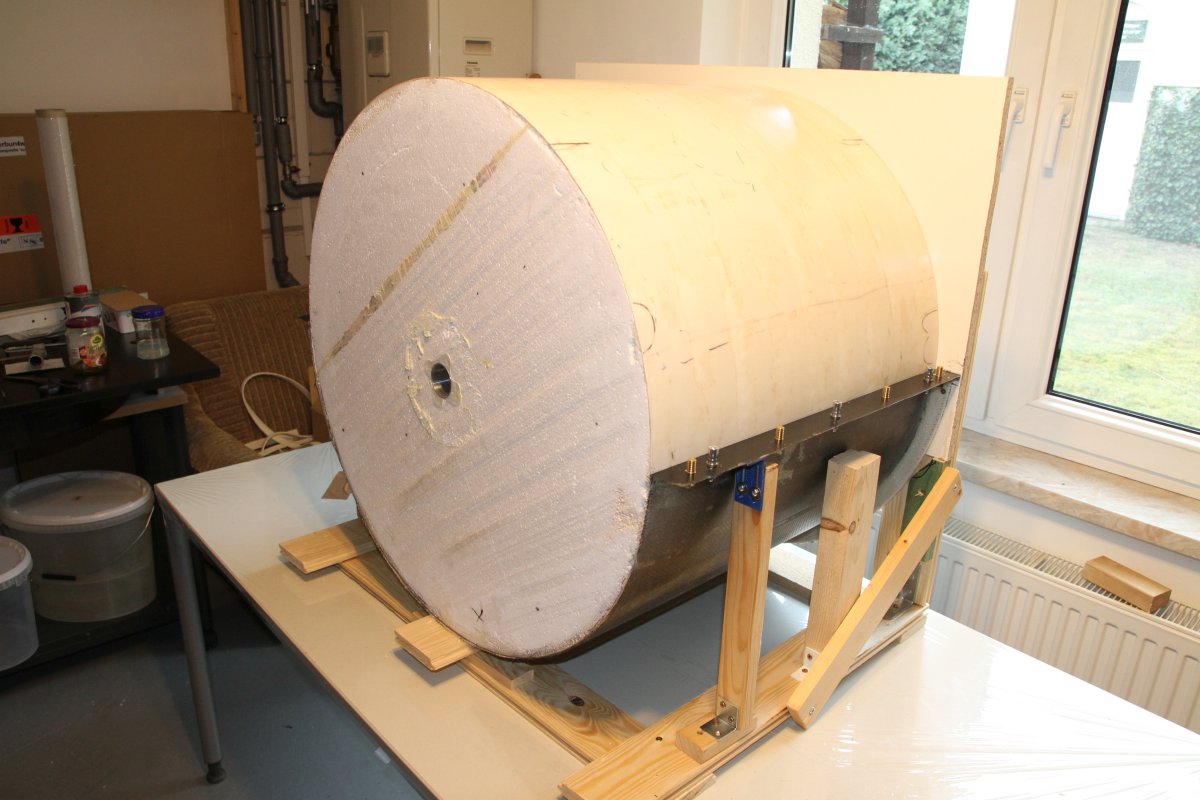
Nach 6maligen wachsen und Aufzug einer PVA-Trennschicht wird nun endlich die Form aus zwei Teilen aufgebaut.

Das Kopfteil des Teleskops soll aus einem CFK Rohr ∅698mm und 500mm Länge bestehen. Also benötige ich eine Teil der gleichen Ausmaße aus Styropor.
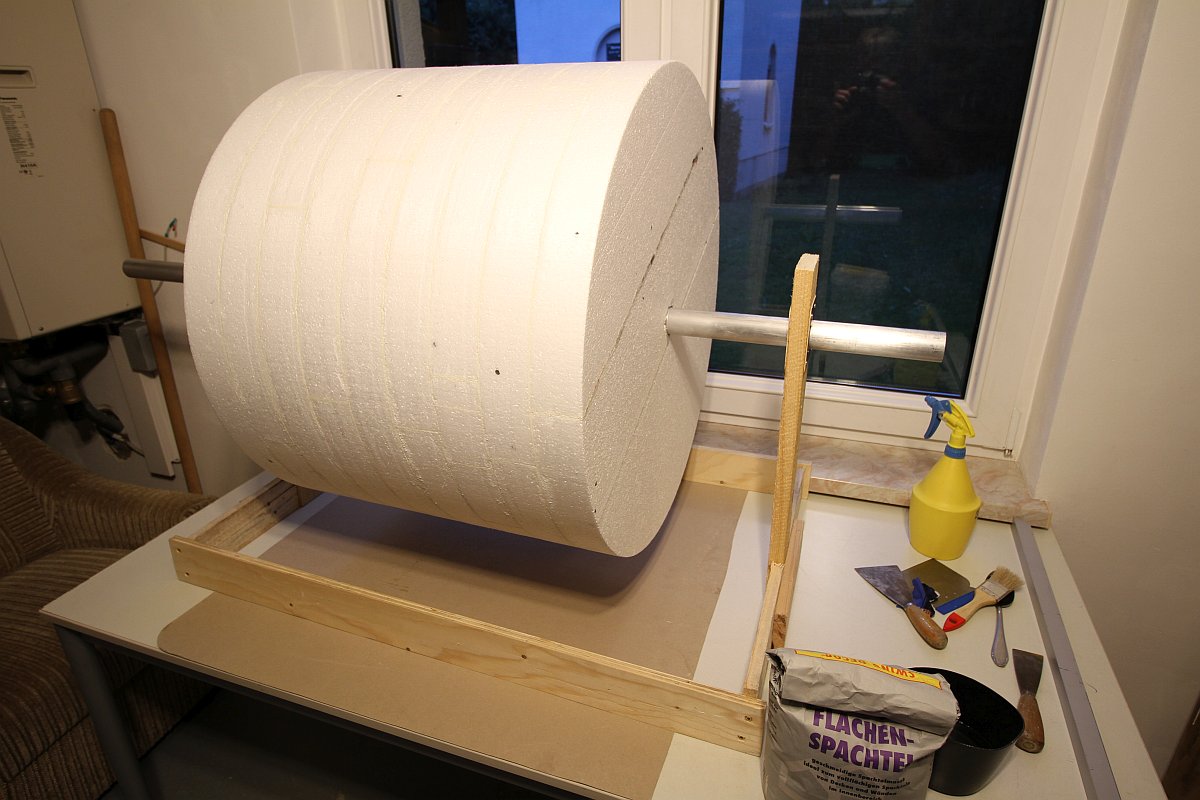
Die groben Unebenheiten werden mit Flächenspachtel für Gipskartinplatten geebnet.
Die Spiegelzelle
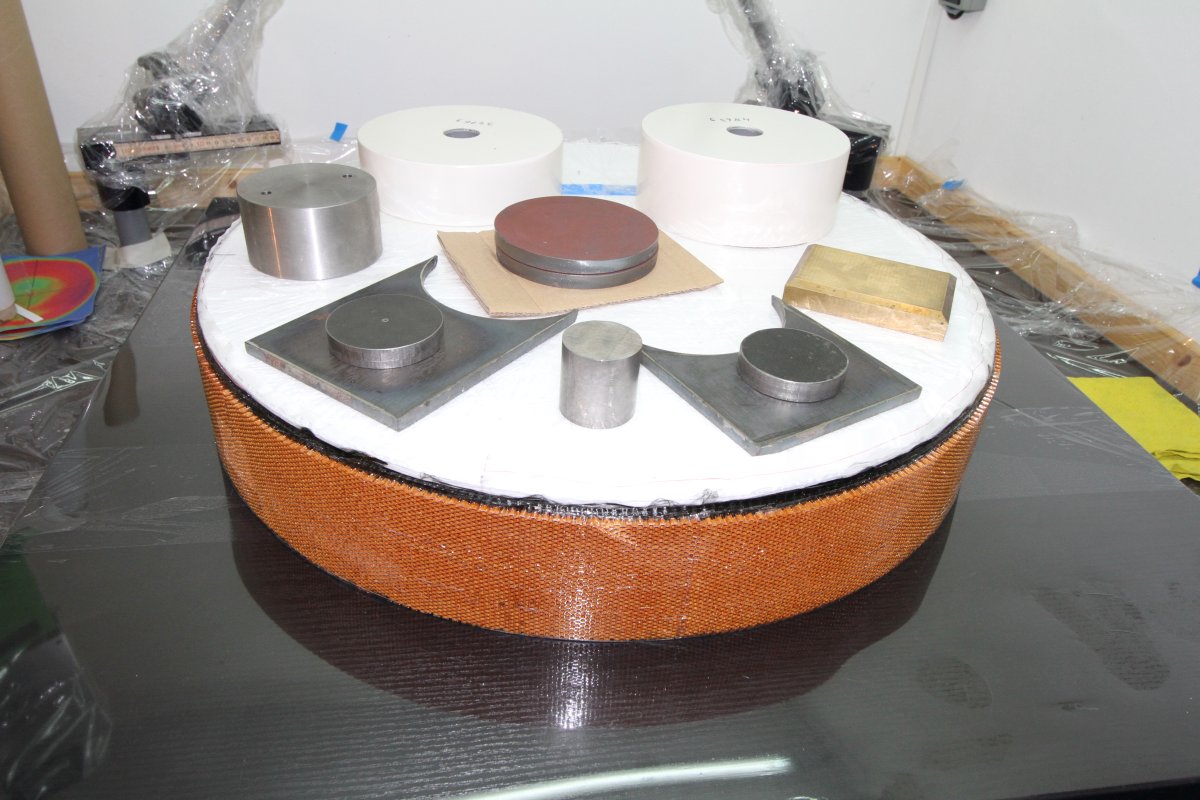
Gut geworden! Der Wabenkern ist gut zzu erkennen und fest verklebt. Nun wird noch eine 2mm Schicht Kohlefaser unidirektional darumgewickelt, natürlich mit 160g/m² Leinen als Kupplungsschicht zwischen Wabe und Kohle.
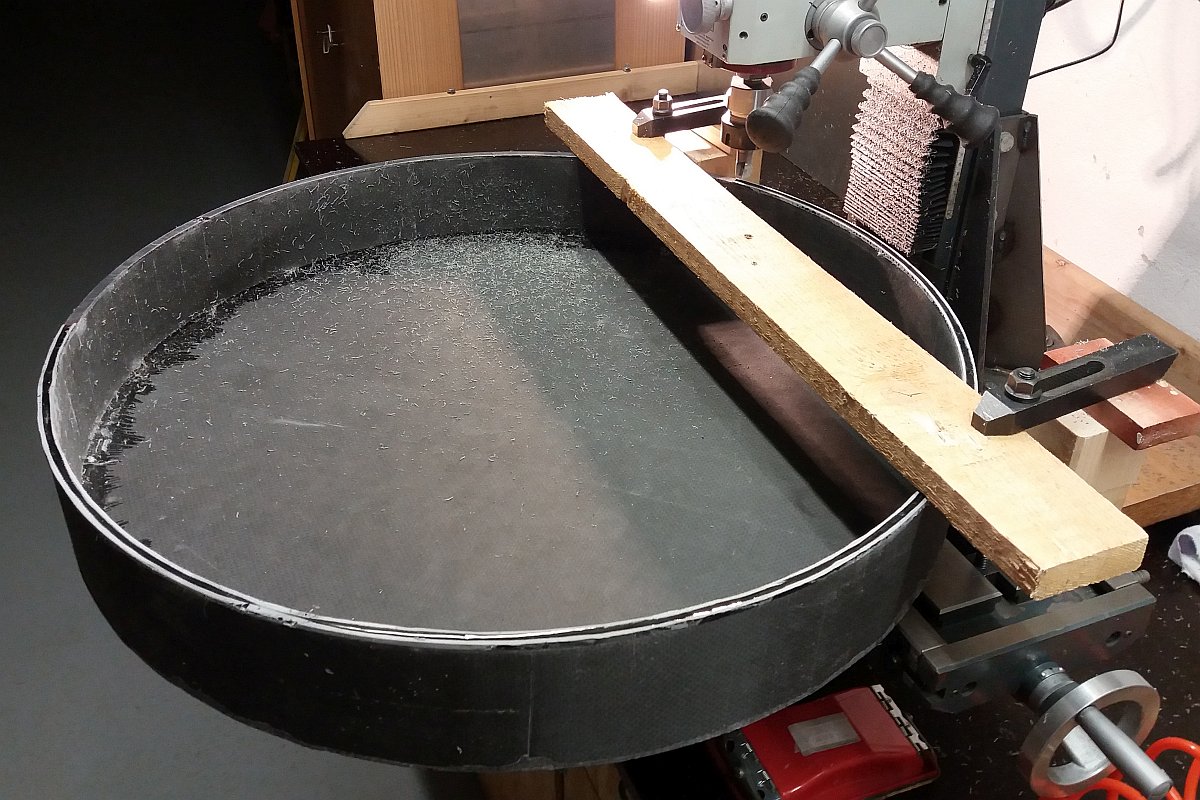
Der Rand wurde einfach mit schwarz gefärbten Harz aufgegossen und nun maßhaltig abgefräßt.
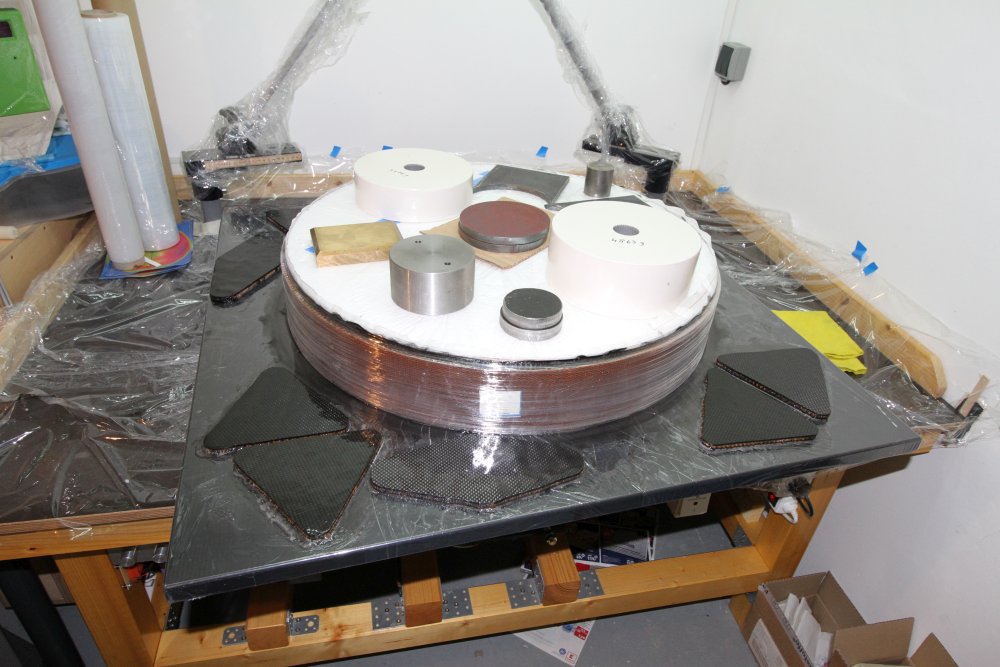
Der Ring um die Bodenplatte bekommt den gleichen Schichtaufbau wie die Platte. Hier habe ich gleich noch die Seiten der Wippenteile mit versiegelt, etwas Thixotropiermittel macht aus dem flüssigen Epoxidharz eine schöne Spachtelmasse.
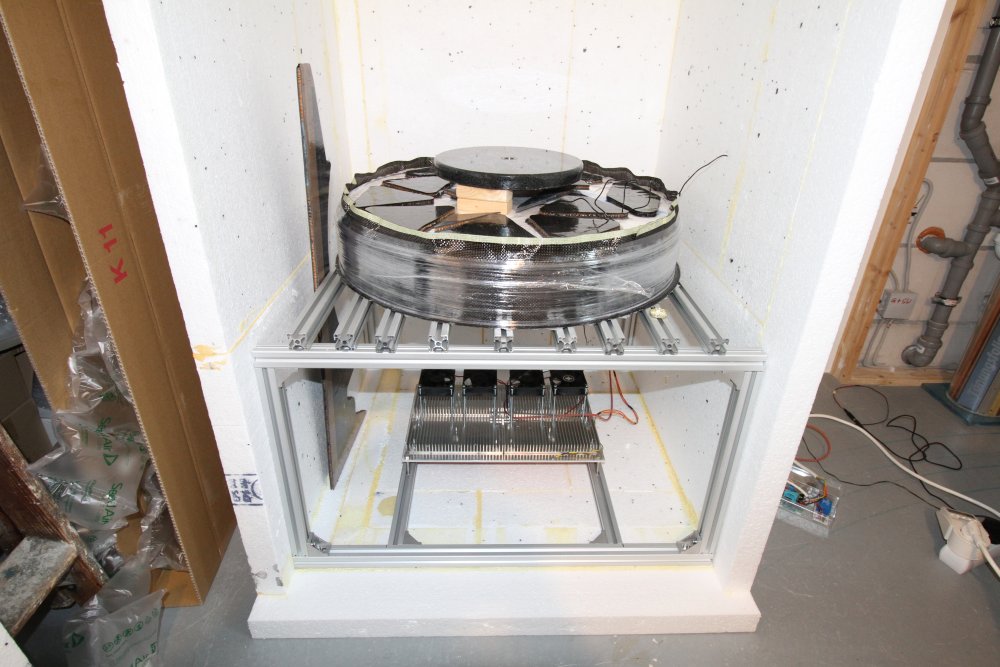
Nun wird alles in den Temperofen geschoben und 24h bei 60°c getempert. Wobei die Temperatur langsam mit 10°C/h erhöht wird. Nebenbai habe ich auch gleich noch mein neues 30cm Granittool zum polieren des großen Spiegels mit Epoxidharz versiegelt.
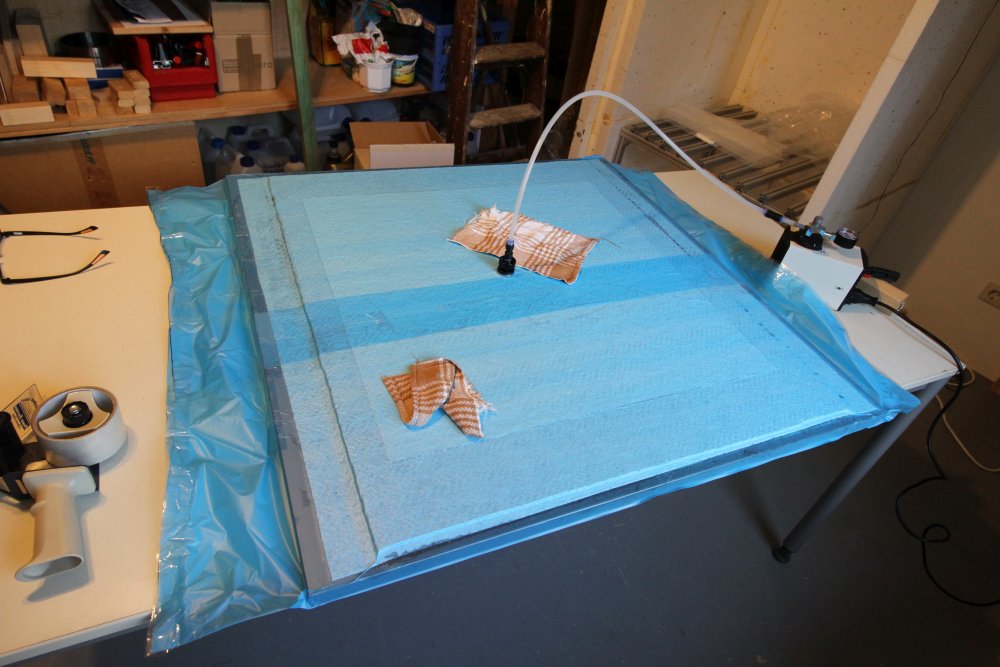
Die ersten 7 Schichten(bis zur Aramid-Wabe) werden mit Epoxidharz aufgebaut und dann im Vakuumpressverfahren 12 Stunden gepresst. Das ist wichtig, um die Aramidwabe ordentlich mit dem Kohlegewebe zu verbinden. Anschließend werden die letzten 6 Schichten aufgebracht und wieder Vakuumgepresst.
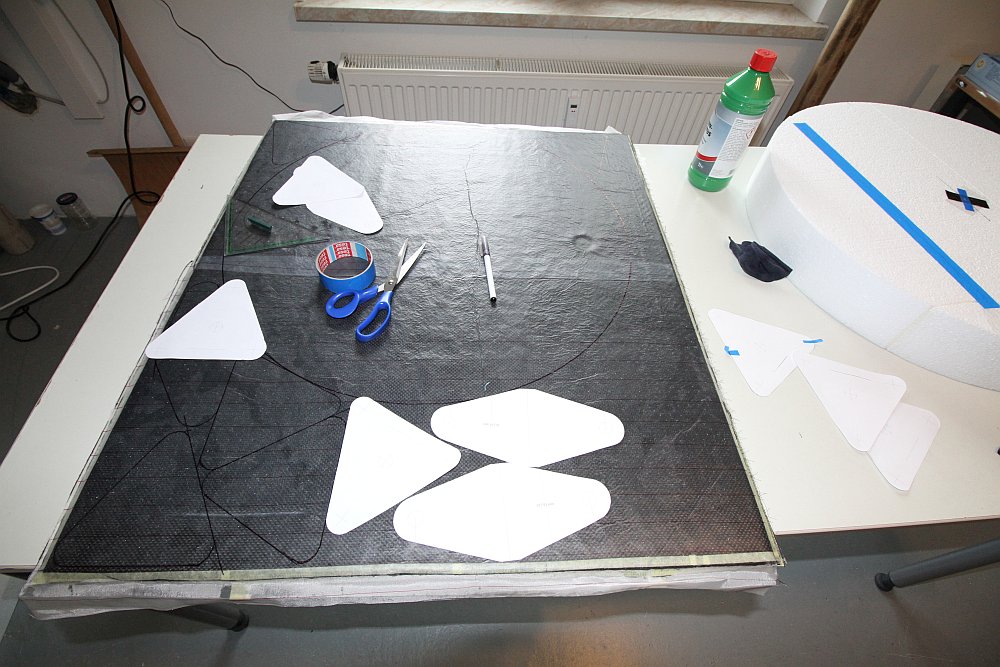
Es ist vollbracht, wir haben eine extrem steife CFK-Platte mit einer Stärke von etwa 10mm. Nun können alle Teile angezeichnet und mit der Stichsäge ausgeschnitten werden.
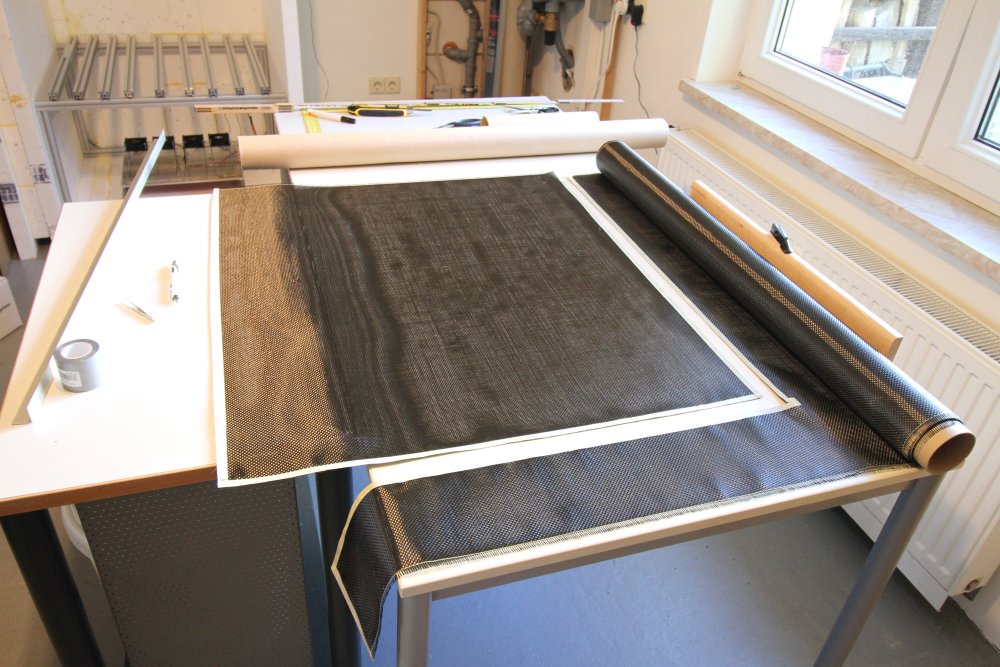
Die Spiegelzelle wird aus CFK gefertigt, als erstes werden die einzelnen Schichten zugeschnitten. Da die verwebten Kohlerovings nur lose aufeinander liegen, ist es vorteilhaft diese vor dem Schneiden mit Klebeband zu sichern. Hier sieht man das 160g/m Leinwand Kohlegewebe.
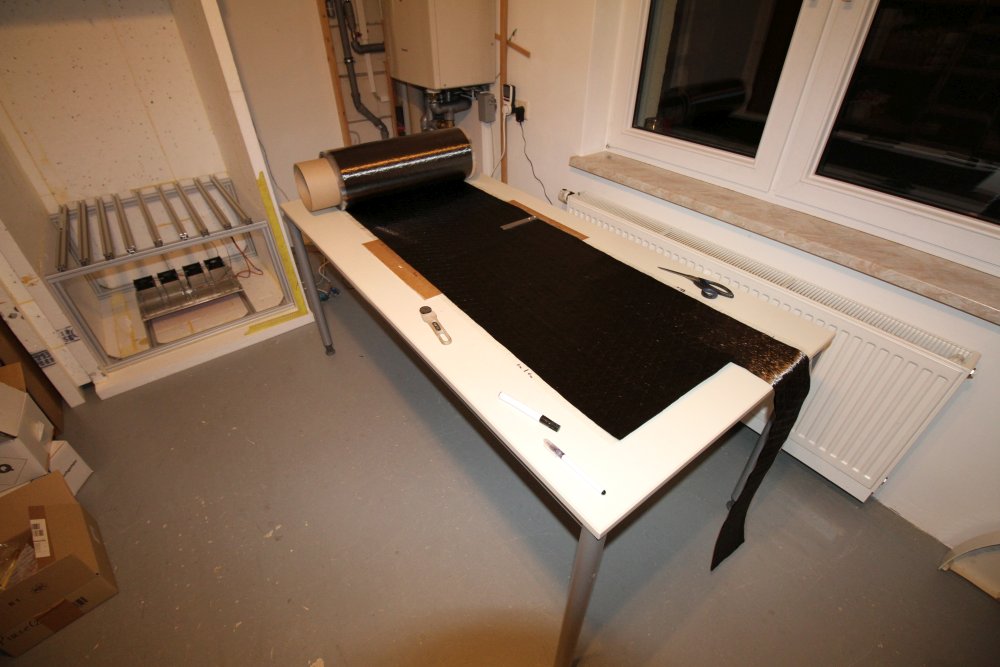
Nun wird noch das 400g/m UD passend geschnitten.
Es wird eine Platte mit folgendem Schichtaufbau:
- 1 Schicht Kohlegewebe 160 g/m² (Leinwand)
- 4 Schichten Kohlegelege ST 400 g/m² (UD)
- 1 Schicht Kohlegewebe 160 g/m² (Leinwand)
- 1 Schicht 5mm Aramid-Wabe
- 1 Schicht Kohlegewebe 160 g/m² (Leinwand)
- 4 Schichten Kohlegelege ST 400 g/m² (UD)
- 1 Schicht Kohlegewebe 160 g/m² (Leinwand)
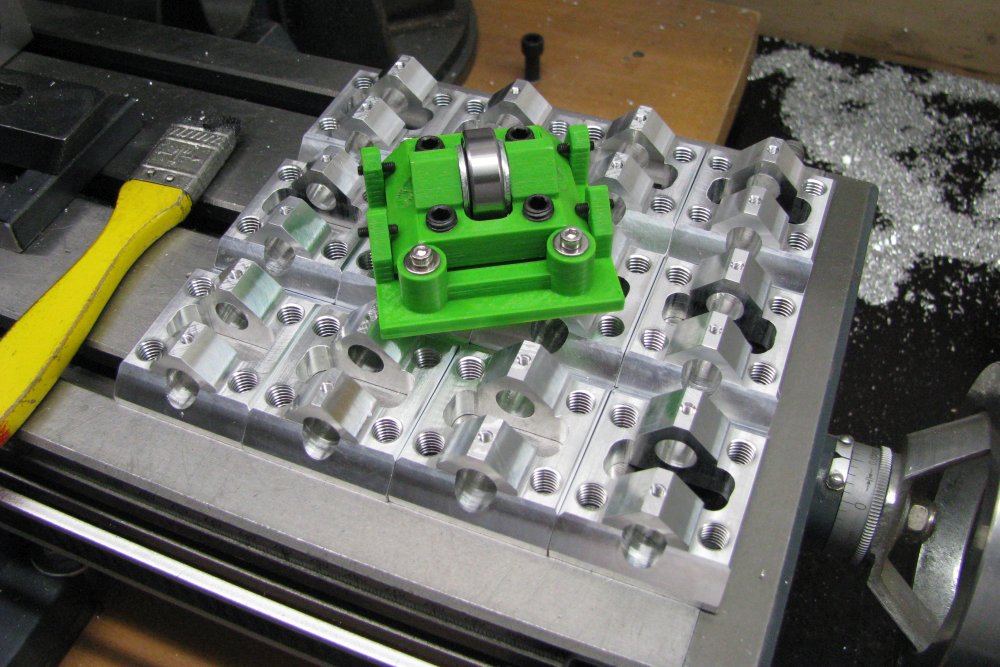
Die 12 Laterallager sind fertig gefräst, darauf liegt die gedruckte Vorlage(grün).
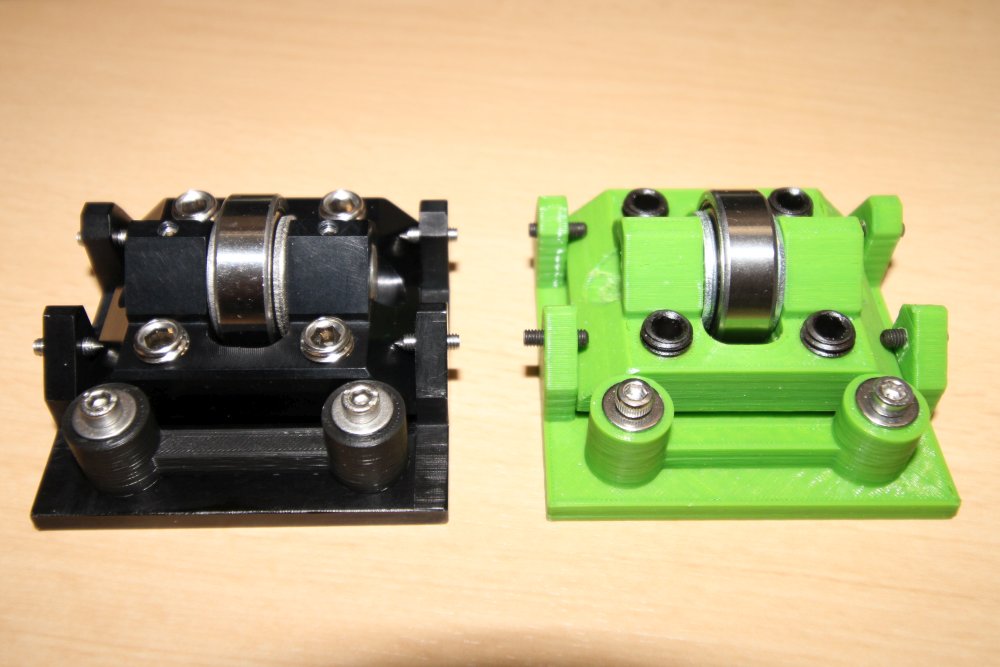
Fertig eloxiert und zusammengebaut.
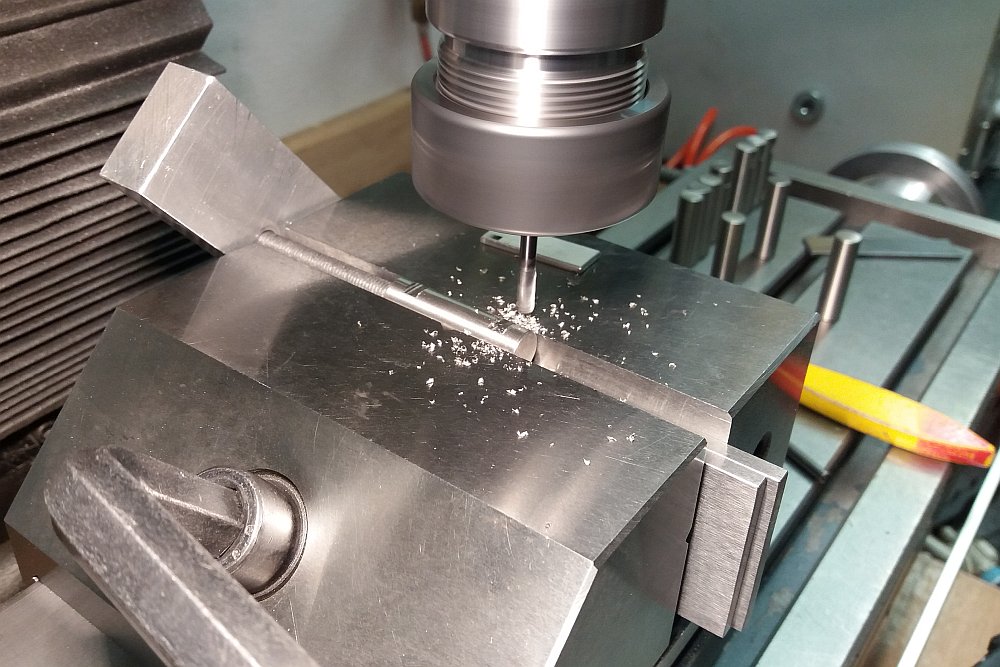
Die Lagerachsen der lateralen Lager, 10mm Edelstahl.
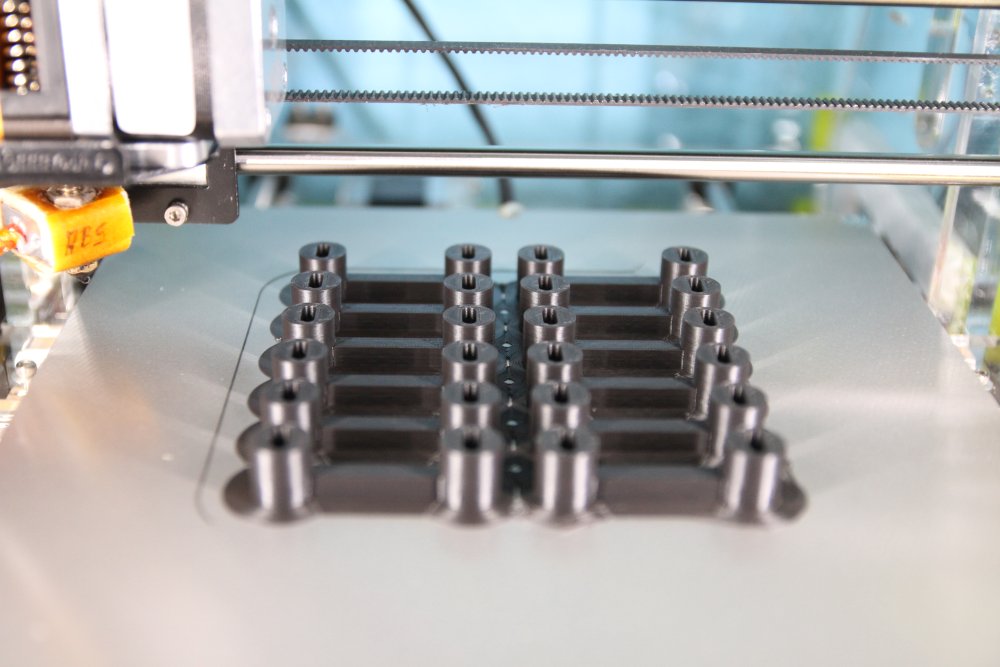
Diese Teile dienen zur einfachen Justage der Lager auf die Schwerelinie des Hauptspiegels, der 3D Drucker kann gleich alle mit einmal aufbauen.
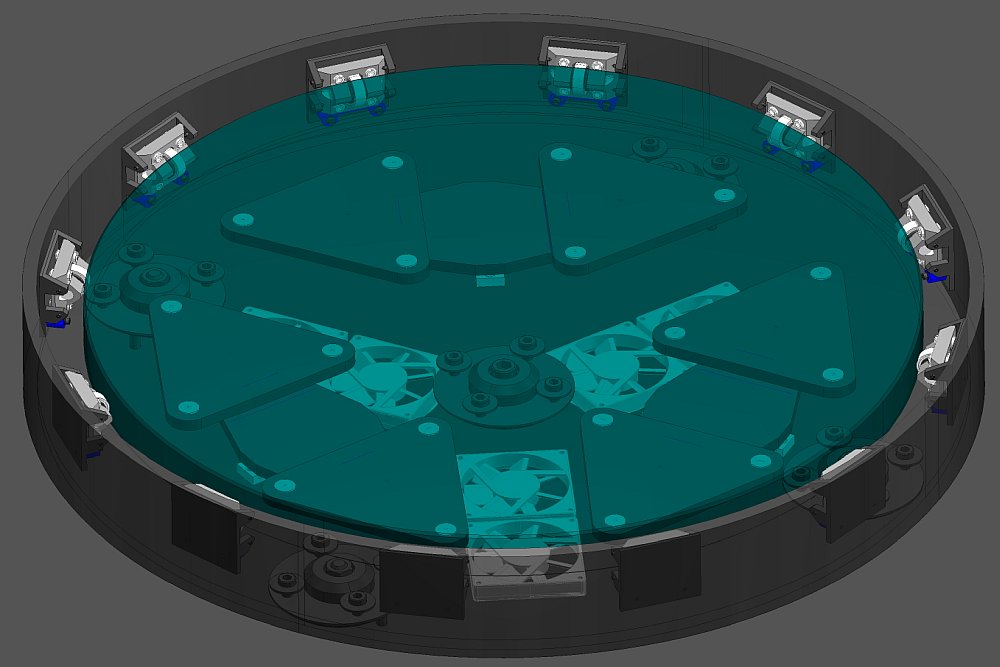
Die Spiegelzelle für den 600mm Spiegel(23kg) ist recht aufwendig. Besonders die laterale Lagerung ist bei equatorialer Montierung kritisch. Meine Lösung ist eine Mischung aus CFK und Mechanik. CFK hat einen Temperaturausdehnungskoeffizient fast Null, was die Gefahr von Verspannungen minimiert.
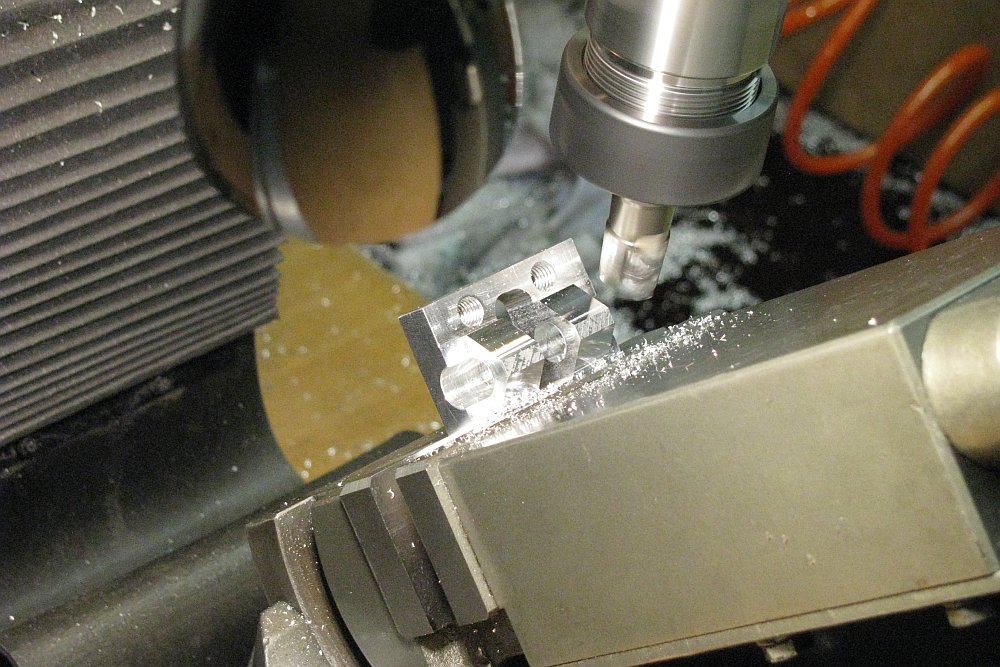
12 mal das gleiche Teil fräsen... ist langweilig aber spart Zeit.
Materiallager
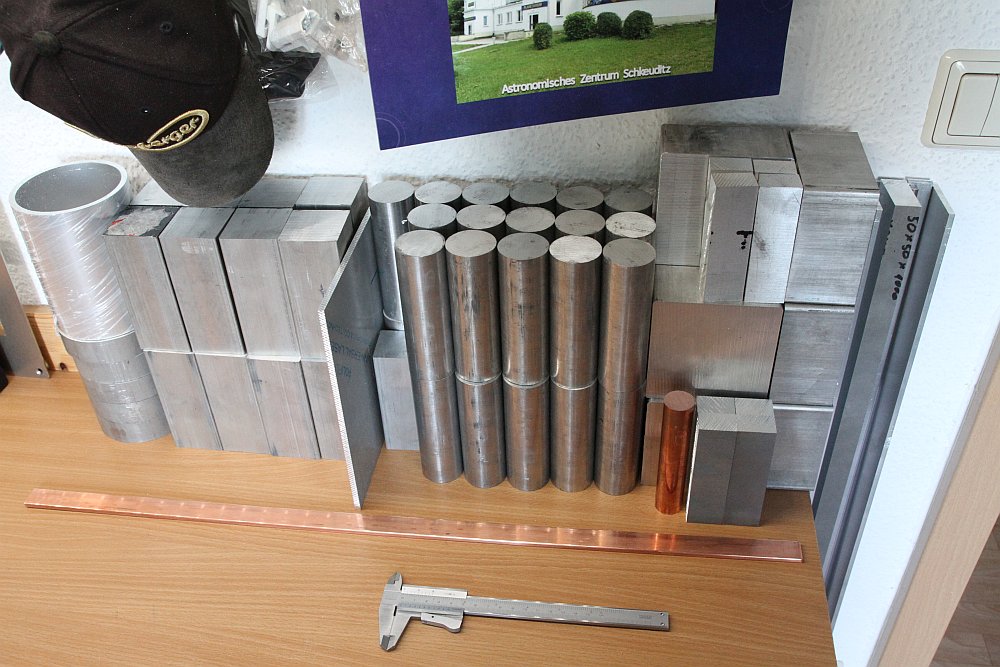
Werkstattsaison ist eröffnet - aus diesen Metallklumpen werden filigrane Teleskopbauteile.
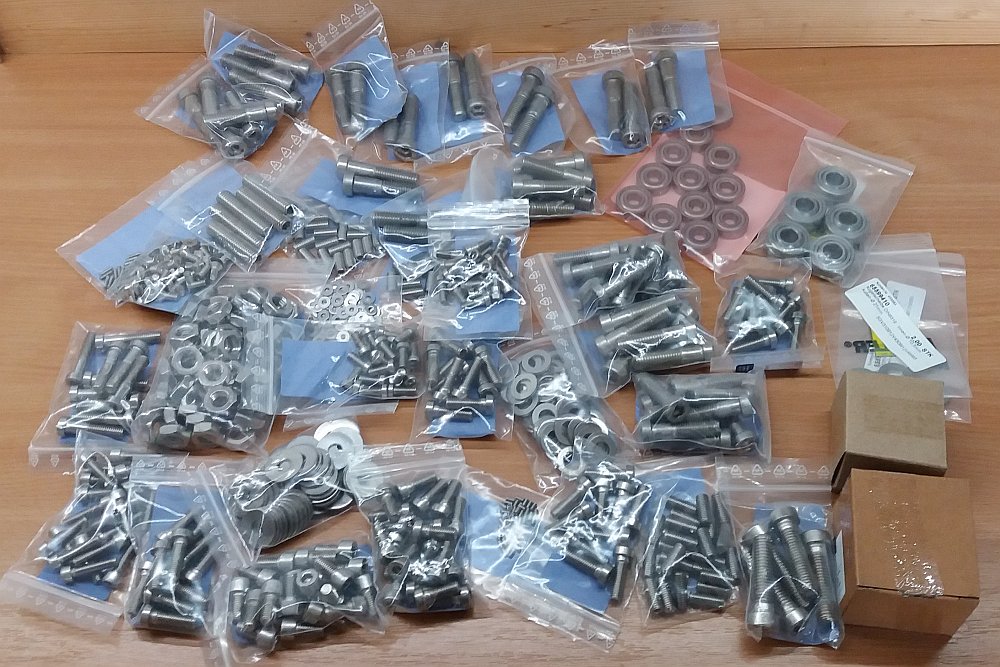
Wenn alles passt, bleibt auch von diesem Haufen nix übrig.
Was schon passiert und eventuell auf anderen Seiten dokumentiert ist:
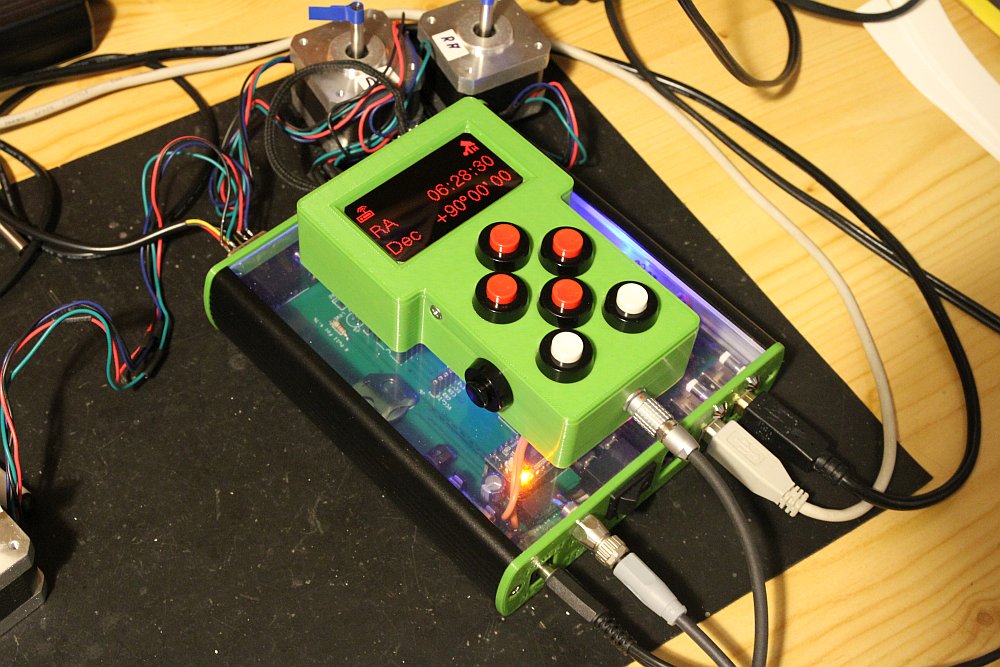
Bau von zwei Steuerungen. Die TeenAstro läuft seit Mai 2019 am 40cm Newton und die zweite ist für das 600mm Projekt vorgesehen. Ein ausdrückliches Dankeschön an das Entwicker-Teem um Charles Lemaire.
TeenAstro Projekt LINK
TeenAstro Astronomie.de LINK
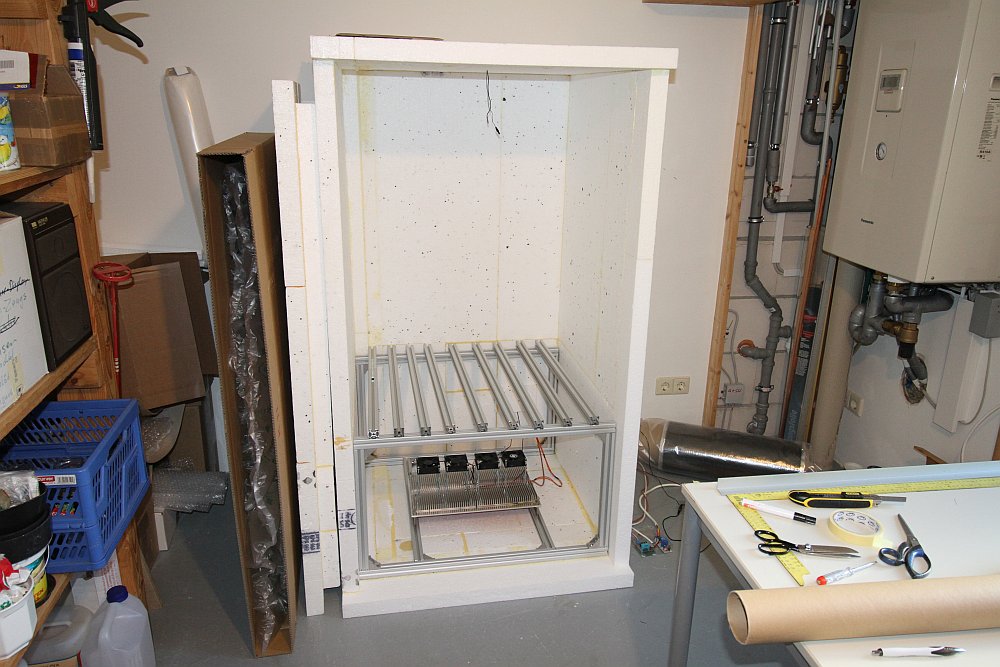
Da nun auch ein paar größere Teile aus CFK gefertigt werden müssen, habe ich meinen Temperofen erweitert.
Rauminhalt: 800mm x 800mm x 1500mm
Temperatur: geregelt bis 80°C
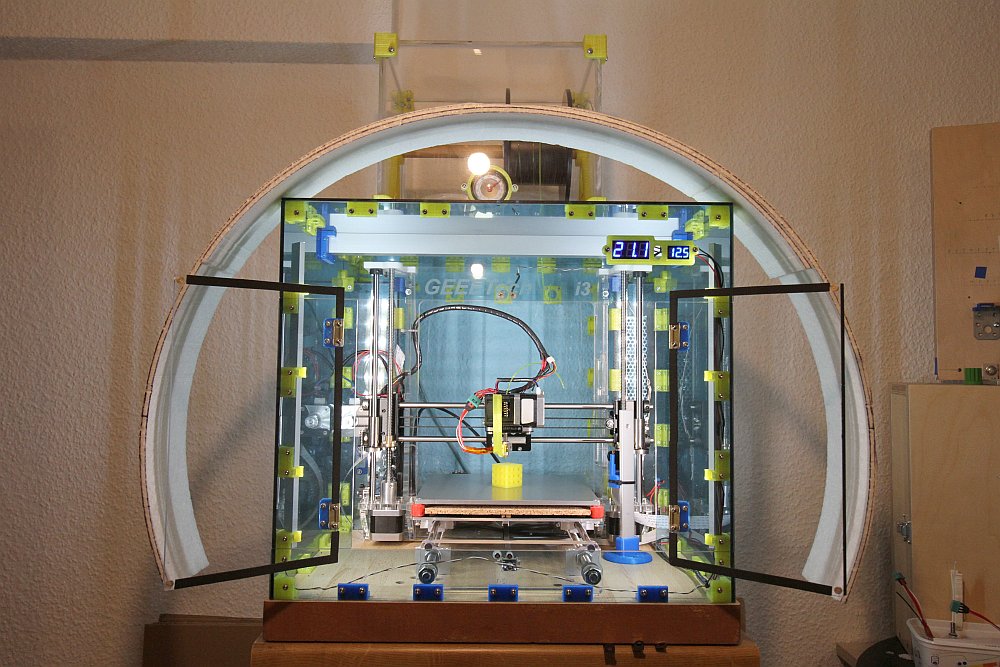
Bau eines 3D Druckers. Neue Fertigungsmöglichkeiten.
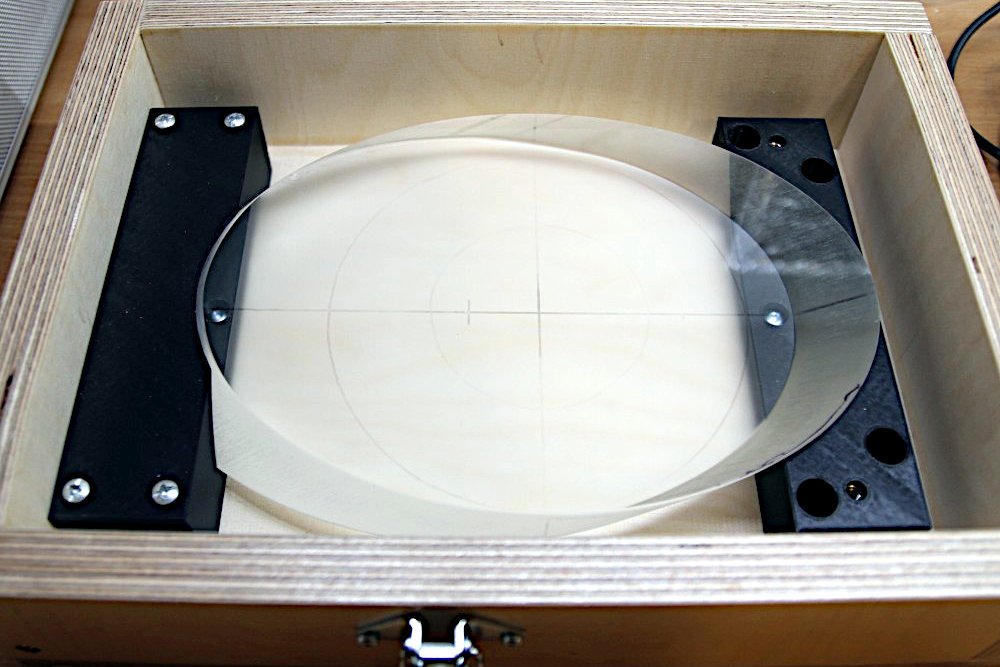
Anfertigung des Ablenkspiegels des 600mm-Newton. Maße: Kleine Achse: 155mm, Große Achse: 220mm, Breite: 25mm
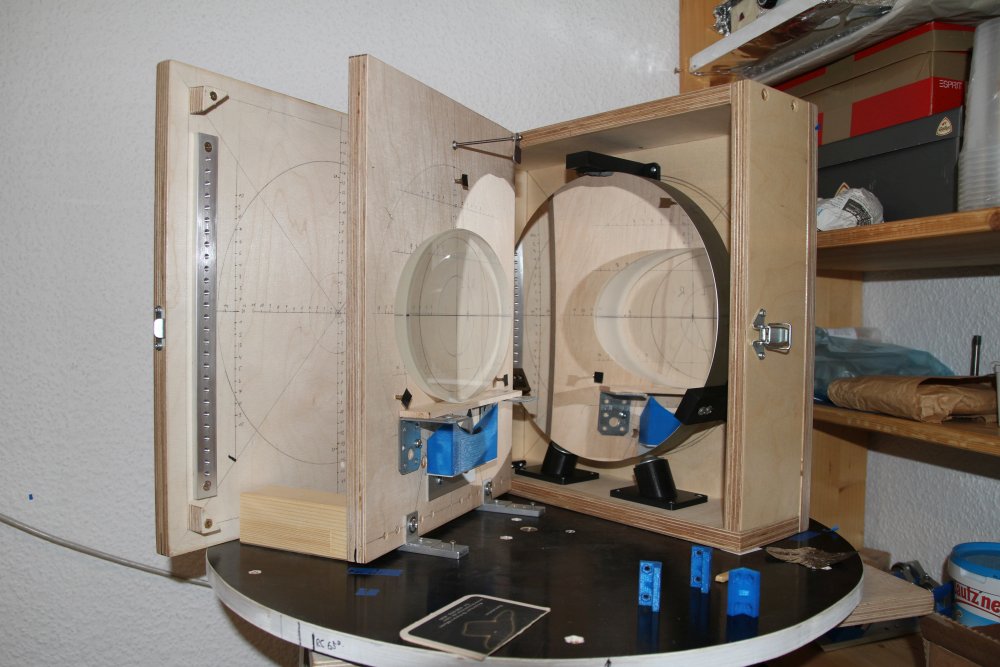
Anfertigung einer hochgenauen Prüfsphäre zum prüfen von Planspiegeln bis 290mm Durchmesser. Spiegeldaten:
- Durchmesser: 300mm, Dicke: 41mm
- ROC: 3003mm
- Randdicke: 37mm
- Laut letzter FFT Messsession mit insgesamt 48 Interferogrammen in 8 Stellungen:
- Strehl:0,998
- RMS wavefront:1/148
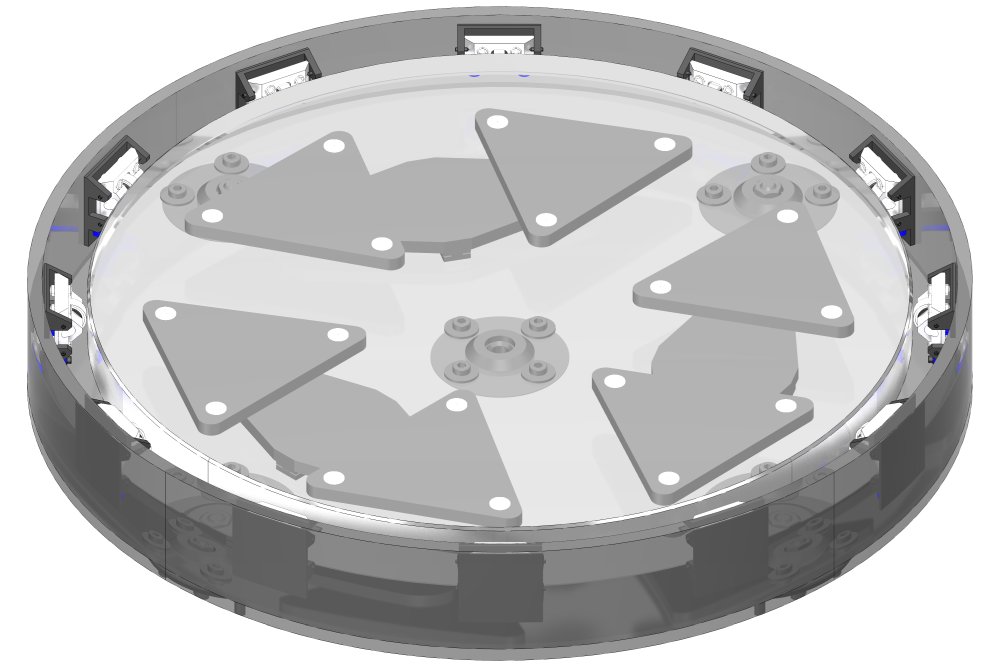
Start der Entwicklung des 3D CAD-Modells zum Bau des Teleskops.
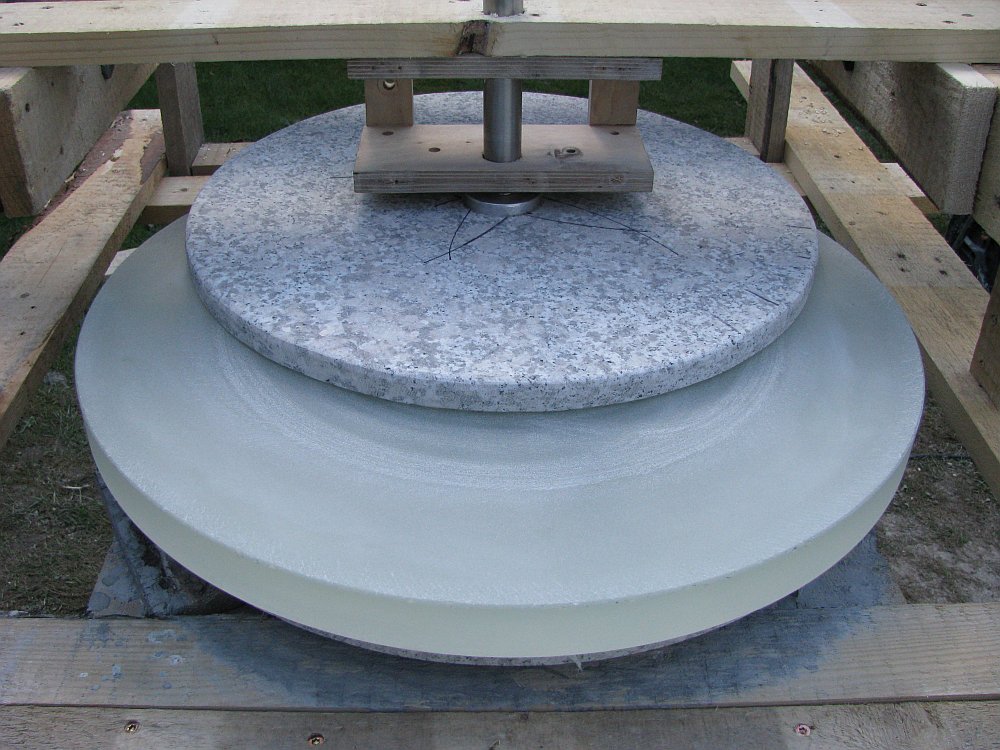
Grobschliff-Feinschliff der Rohlinge: 600/40-Hauptspiegel, 305/45-Prüfsphäre, 270/250-Planspiegel
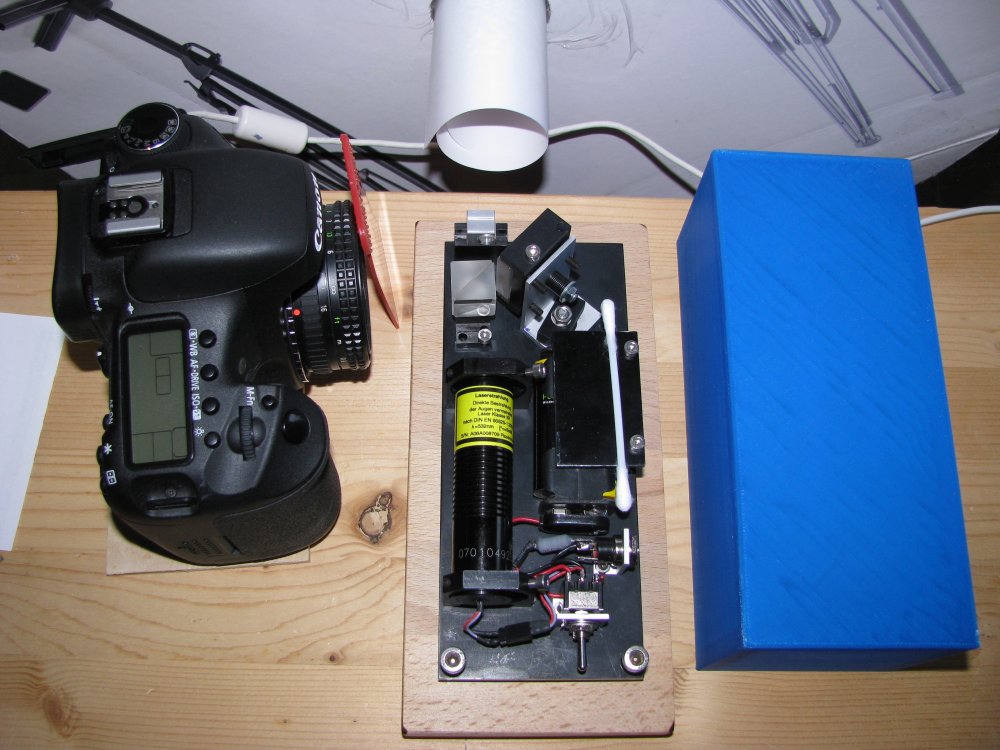
Bau und Test des Bath-Interferometer